adbuch wrote: Sun Oct 20, 2024 1:27 am
Kwikvette - Those are some nice looking cuts and bends! Do you feel that you are getting better cut quality with the 45xp than you had with your Primeweld 60? I like your bench top press brake. I built something similar using a HF 20 ton hydraulic press and the Swag Offroad kit. I added the HF air-over-hydraulic 20 ton bottle jack for bending the thicker stuff.
To see all photos - click on this link.
https://photos.app.goo.gl/B8fQSKZZPo15u6je9
David
20220628_222428_resized.jpg
20220628_222500_resized.jpg
20220628_222626_resized.jpg
grizzly dies with adapters.jpg
Thanks!
Bit of a loaded question but I'll try my best
So far, outside of test cuts, I haven't done much on the Hypertherm outside of the few production pieces I just did yesterday. With that said, I do have a master set of this production run I keep that I use for "quality control" and I have to say, the PrimeWeld was actually cutting quite a bit better. I attribute this to just needing to dial in my 45XP a bit since book isn't exactly best but for now, what I'm seeing gets me there.
I did perform multiple test runs on 16 gauge with varying results - on a small test square, regardless of the amp setting or speed, I got massive beveling all the way around. Whether it was book at 45 amps and 239ipm, or something I tested on my own like 35 amps and 150ipm, I got massive beveling and some dross although book settings got me the least amount of dross surprisingly enough. I won't do more test cuts for 16 gauge and will simply purchase fine cut for that purpose.
Speaking of benders, I used to run the Swag Offroad heavy duty kit with Harbor Freight press as well some years ago. It did "alright" in my opinion but I absolutely hated the angle iron used as a bottom die. Even stacking angle iron didn't allow me to run as small of a flange as I wanted paired with the large punches used. I had gone as far as even cutting my own punches via CNC until I decided to just get rid of the whole thing.
I had it long before they came up with that adjustable bottom die you're running, and opted for something more compact until I build my own.
My old setup -
I mean, even with its large bend radius, it did help me knock out larger parts when I needed it to -
And that "master" piece I mentioned above that was cut on the PrimeWeld CUT60, and bent on my smaller press brake -
Although the brake only has a working width of 10", it uses a nice 4-way bottom block and a 30 degree punch which really let's me make small parts for others -
Or for myself even -
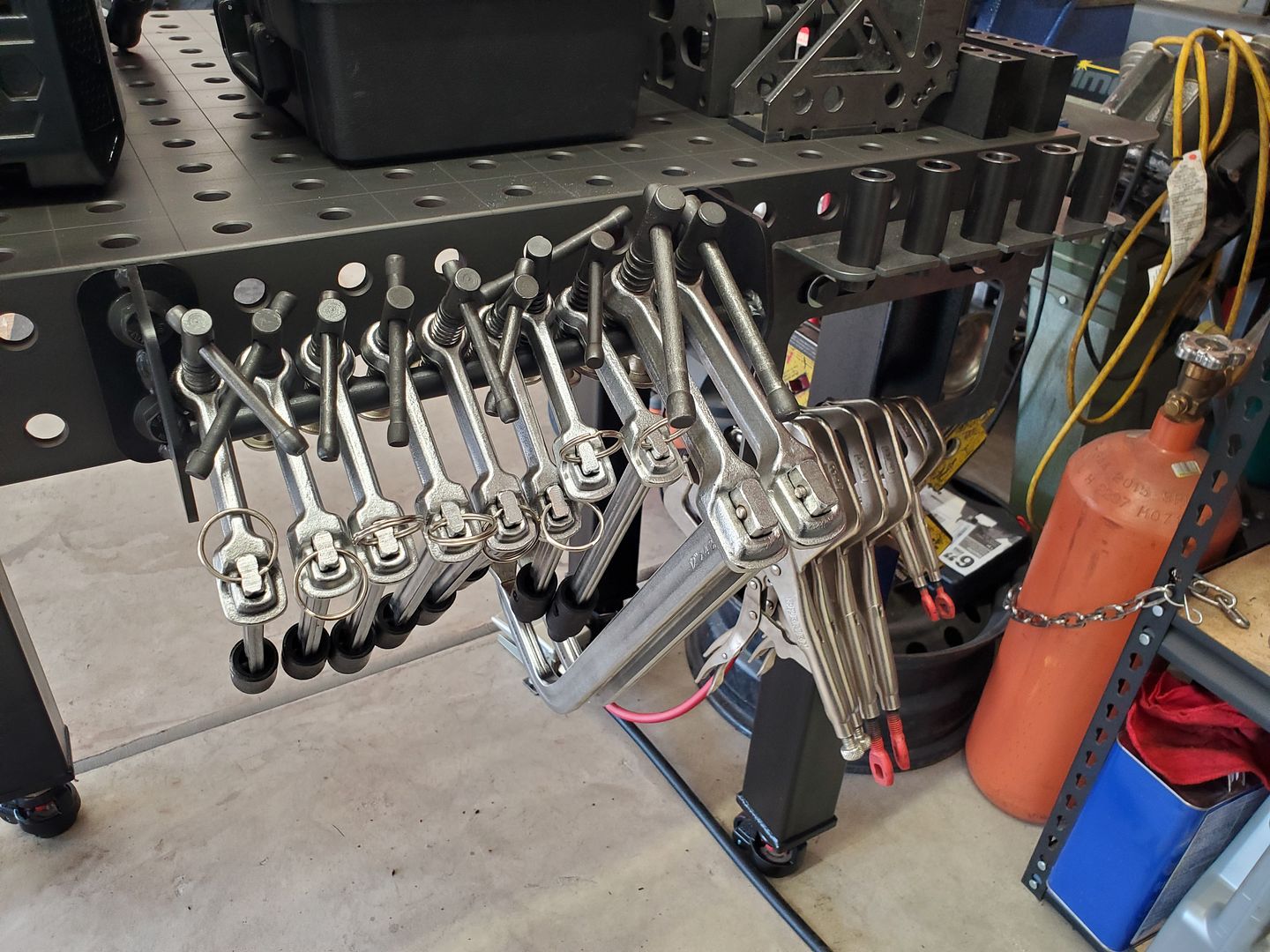