First 12mm cuts tonight...
-
- 4 Star Member
- Posts: 764
- Joined: Wed Aug 13, 2014 8:30 am
- Location: Hertfordshire, England
- Contact:
First 12mm cuts tonight...
Following on from the tips given in another thread on 12mm (thanks SeanP) I cut my first parts in 12mm tonight, learnt a few things too.
The settings ended up at...
45A
120v
1.3mm kerf
1.2s pierce delay
510mm/min speed
4mm pierce height
1.5mm cut height
Front and back of the parts... Edge detail in the notches... The notches exhibited the usual tail lag in the bottom corners, is there anything that can help this?
The tops of the notches were squared up by using loops on the path, this however caused me to waste a chunk on the first trial when the two loops touched and made the bit in the middle drop out - when the torch reached the 2nd loop it was cutting in air and turned itself off. I realised the error and altered the file for smaller loops that did not touch, this fixed it nicely but as it was running you could see the torch dive at each loop, just enough to touch the plate, not enough to cut the arc so i let it run. Maybe i'll turn the THC off on loops in future.
Minimal dross and it fell of easily, edge angularity was perfect, hole taper was acceptable, I still have issues with divots though, even on this thickness. Even though i gave a little overburn it still left a little tag at the bottom of the exit path.
Overall, I am mightily impressed, this came out better than my 3mm stuff, wouldn't mind doing more when i can.
The settings ended up at...
45A
120v
1.3mm kerf
1.2s pierce delay
510mm/min speed
4mm pierce height
1.5mm cut height
Front and back of the parts... Edge detail in the notches... The notches exhibited the usual tail lag in the bottom corners, is there anything that can help this?
The tops of the notches were squared up by using loops on the path, this however caused me to waste a chunk on the first trial when the two loops touched and made the bit in the middle drop out - when the torch reached the 2nd loop it was cutting in air and turned itself off. I realised the error and altered the file for smaller loops that did not touch, this fixed it nicely but as it was running you could see the torch dive at each loop, just enough to touch the plate, not enough to cut the arc so i let it run. Maybe i'll turn the THC off on loops in future.
Minimal dross and it fell of easily, edge angularity was perfect, hole taper was acceptable, I still have issues with divots though, even on this thickness. Even though i gave a little overburn it still left a little tag at the bottom of the exit path.
Overall, I am mightily impressed, this came out better than my 3mm stuff, wouldn't mind doing more when i can.
- BTA Plasma
- 3.5 Star Elite Contributing Member
- Posts: 617
- Joined: Thu May 12, 2011 4:28 pm
Re: First 12mm cuts tonight...
Dave so you can loop corners and get outside corners to look great but for inside you cannot rely on acceleration rates alone you need to use your CV settings as well. You can use the stop at CV angles setting in the config/general settings to help with inside corners. Plasma will have a trailing edge and will need a slight delay to catch up. But be warned that the trailing edge angle changes with beam strength and when it catches up to the travel you have already blown away more material at the top of the cut. You cannot get a very very very good inside corner with an air cooled plasma unless your using a path rule with CandCNC's DCC where you boost amperage just near the corner then drop it as you move out. If you have the RS485 and CandCNC's DCC set up you can get much better corners than with CV settings and definitely just acel, decel alone.
- BTA Plasma
- 3.5 Star Elite Contributing Member
- Posts: 617
- Joined: Thu May 12, 2011 4:28 pm
Re: First 12mm cuts tonight...
You can also try geometric changes like this by offsetting a toolpath in CAD half the kerf width and adding a small corner angular back up. It is more complex to do this but man does it work!
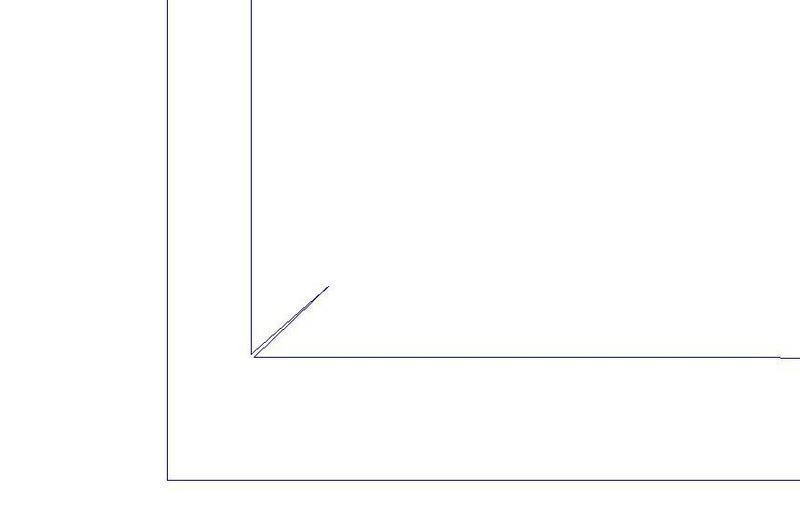
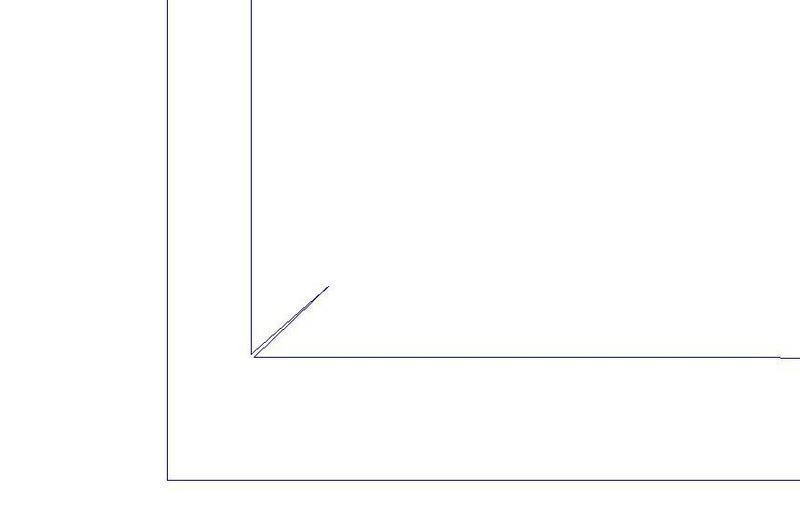
-
- 4 Star Member
- Posts: 764
- Joined: Wed Aug 13, 2014 8:30 am
- Location: Hertfordshire, England
- Contact:
Re: First 12mm cuts tonight...
BTA Plasma wrote:You can also try geometric changes like this by offsetting a toolpath in CAD half the kerf width and adding a small corner angular back up. It is more complex to do this but man does it work!
That sounds interesting, can you elaborate on the half kerf bit please?
I have tried messing with CV/angles but while it sort of worked, it did not give the result wanted, as you say - it eats into the top face.
I also tried a path rule to drop to 60% speed but it created a divot where the speed dropped and accelerated - again undesired.
Luckily, I had the sense to advise the customer of these little issues and just as luckily he had already had parts plasma cut and acknowledged that it was not perfect.

-
- 4 Star Member
- Posts: 764
- Joined: Wed Aug 13, 2014 8:30 am
- Location: Hertfordshire, England
- Contact:
Re: First 12mm cuts tonight...
BTA Plasma wrote:You can also try geometric changes like this by offsetting a toolpath in CAD half the kerf width and adding a small corner angular back up. It is more complex to do this but man does it work!
That sounds interesting, can you elaborate on the half kerf bit please?
I have tried messing with CV/angles but while it sort of worked, it did not give the result wanted, as you say - it eats into the top face.
I also tried a path rule to drop to 60% speed but it created a divot where the speed dropped and accelerated - again undesired.
Luckily, I had the sense to advise the customer of these little issues and just as luckily he had already had parts plasma cut and acknowledged that it was not perfect.

- BTA Plasma
- 3.5 Star Elite Contributing Member
- Posts: 617
- Joined: Thu May 12, 2011 4:28 pm
Re: First 12mm cuts tonight...
If you offset and build in a lead in and lead in your cad drawing out you can cut with no offset in sheetcam. It takes more CAD to make a very very square corner with a plasma cutter but you can do it. What this will do is go to the edge of the corner and back out then lead in to the other edge so the other edge will be strait and not have a trailing edge.
-
- 4 Star Member
- Posts: 764
- Joined: Wed Aug 13, 2014 8:30 am
- Location: Hertfordshire, England
- Contact:
Re: First 12mm cuts tonight...
Got it, thanks.
Not sure how i would implement it yet but the idea makes sense. I guess if the CAD has an expand feature it would work, mine does not, but might be other ways...
Not sure how i would implement it yet but the idea makes sense. I guess if the CAD has an expand feature it would work, mine does not, but might be other ways...
- BTA Plasma
- 3.5 Star Elite Contributing Member
- Posts: 617
- Joined: Thu May 12, 2011 4:28 pm
Re: First 12mm cuts tonight...
Dave when ever you see a edge like that you can over come it with some enhanced geometry changes. It is for more experienced folks that like to perfect the end result. Most folks will just tell them 'that's what you get when you plasma cut'. But you can get even better results. Look at the other corner, it looks great.
-
- 4 Star Member
- Posts: 764
- Joined: Wed Aug 13, 2014 8:30 am
- Location: Hertfordshire, England
- Contact:
Re: First 12mm cuts tonight...
Why is the other corner better?
- BTA Plasma
- 3.5 Star Elite Contributing Member
- Posts: 617
- Joined: Thu May 12, 2011 4:28 pm
Re: First 12mm cuts tonight...
Most likely due to mechanical play in your Y or X axis or it may be a result of HAZ from looping that outer edge.
-
- 3.5 Star Member
- Posts: 511
- Joined: Wed Apr 23, 2014 2:48 pm
Re: First 12mm cuts tonight...
This is a case where more power is better.. (IMO) The arc just is more powerful does not lag as much. I would rather cut 0.500" at 65 amps(30 ipm) or 70 amps (32 ipm) on my Esab. My friend cuts ton of this stuff, and very minimal issues.(Very nice too) Victor was nice at 70 amps too..
- SeanP
- 4 Star Member
- Posts: 951
- Joined: Thu Aug 01, 2013 11:50 am
- Location: Co Kerry, Ireland
Re: First 12mm cuts tonight...
The cut rules work great for the loop corners Dave, 1.5mm arc is plenty big enough for 12mm thick I have found.
Cut's look great, I get just the same on sharp internal corners, like mentioned there I reckon it's just the power/amps of the machine and the nature of plasma cutting.
Did you not manage to save the part Dave? I seem to be doing fairly well at restarting after a cock up, been plenty of them maybe that's how!
How I re start:
Go back to M05 for cut to restart.
Set next line
Ref Z (but don't zero)
Turn off THC button
Run
As soon as torch fires, switch torch off ( I have a keyboard button for this)
Just before torch comes around to the failed part of the cut switch torch back on (hopefully cut height is somewhere near at that point)
Once cut establishes switch thc button back on and away you go, saved loads of parts that way.
Again that little tag gets me also, holes mostly seem to drop ok though well up to 25mm dia, with the base plates though safest bet for me was adding that 50% slowdown rule for a couple of mm where it crossed the leadout, I was leadin/out on a corner there.
Ahh you done a fine job there Dave!
Cut's look great, I get just the same on sharp internal corners, like mentioned there I reckon it's just the power/amps of the machine and the nature of plasma cutting.
Did you not manage to save the part Dave? I seem to be doing fairly well at restarting after a cock up, been plenty of them maybe that's how!
How I re start:
Go back to M05 for cut to restart.
Set next line
Ref Z (but don't zero)
Turn off THC button
Run
As soon as torch fires, switch torch off ( I have a keyboard button for this)
Just before torch comes around to the failed part of the cut switch torch back on (hopefully cut height is somewhere near at that point)
Once cut establishes switch thc button back on and away you go, saved loads of parts that way.
Again that little tag gets me also, holes mostly seem to drop ok though well up to 25mm dia, with the base plates though safest bet for me was adding that 50% slowdown rule for a couple of mm where it crossed the leadout, I was leadin/out on a corner there.
Ahh you done a fine job there Dave!
Powermax XP45
Home built table, Candcnc DTHC 2, Dragoncut 620-4
R-Tech 210 Tig, Jasic 250 mig
Sheetcam, Scanything, Coreldraw
Table build gallery
Home built table, Candcnc DTHC 2, Dragoncut 620-4
R-Tech 210 Tig, Jasic 250 mig
Sheetcam, Scanything, Coreldraw
Table build gallery
- SeanP
- 4 Star Member
- Posts: 951
- Joined: Thu Aug 01, 2013 11:50 am
- Location: Co Kerry, Ireland
Re: First 12mm cuts tonight...
Nice tip there, might have a try at that.
BTA Plasma wrote:You can also try geometric changes like this by offsetting a toolpath in CAD half the kerf width and adding a small corner angular back up. It is more complex to do this but man does it work!
Powermax XP45
Home built table, Candcnc DTHC 2, Dragoncut 620-4
R-Tech 210 Tig, Jasic 250 mig
Sheetcam, Scanything, Coreldraw
Table build gallery
Home built table, Candcnc DTHC 2, Dragoncut 620-4
R-Tech 210 Tig, Jasic 250 mig
Sheetcam, Scanything, Coreldraw
Table build gallery
-
- 4 Star Member
- Posts: 764
- Joined: Wed Aug 13, 2014 8:30 am
- Location: Hertfordshire, England
- Contact:
Re: First 12mm cuts tonight...
Thanks all,
I have no option to get a bigger unit as no power or air for it.
There is no slack at all in my axes, machine is still tight as practically new.
I will use a smaller loop in future;)
I did try rescuing the part as i always do but Mach started going off on a tangent so i gave up, time limits and all that stuff, it was near the beginning so not much steel wasted and i can use the gap created for tests and fine tuning my settings when i get a chance. The job paid for the whole piece anyway so no real loss and a lot learnt.
I have no option to get a bigger unit as no power or air for it.
There is no slack at all in my axes, machine is still tight as practically new.
I will use a smaller loop in future;)
I did try rescuing the part as i always do but Mach started going off on a tangent so i gave up, time limits and all that stuff, it was near the beginning so not much steel wasted and i can use the gap created for tests and fine tuning my settings when i get a chance. The job paid for the whole piece anyway so no real loss and a lot learnt.
-
- 5 Star Elite Contributing Member
- Posts: 3087
- Joined: Mon Jul 20, 2009 11:18 pm
- Location: North Carolina
Re: First 12mm cuts tonight...
Overall the cuts look great. You can improve that lag induced undercut in the notches by experimenting with reducing your machines acceleration settings....this will allow the lag in the arc to catch up with the top of the arc.
As far as hole issues....each cnc machine has different backlash, different flex and different acceleration/speed capabilities based on design, condition and mass. I suggest trying a few different hole lead in configurations as well as lead out configurations to determine what works best for your machine.
Lead ins: start dead center in holes and try straight (90 degree) lead ins. These work best with machines with extremely good acceleration and zero backlash. Curved or tangential lead ins that slowly merge into the hole radius work best on machines with sluggish acceleration and / or backlash. The plasma arc moves around less when it approaches a 90 degree lead in.....has trouble and wiggles a bit when merging with a radial lead in!
Lead outs. More complex high definition class plasma cutters use an overburn that goes a calculated distance (staying on the hole radius) past the lead in kerf......yet shuts the plasma arc off before getting to the lead in kerf. Air (or oxygen) plasma does not instantly extinguish....so the CAM software on more complex systems uses its data files to time the shutoff of the arc (based on power level, material thickness and hole diameter) to eliminate the divot caused by the arc extinguishing too soon (an inner "ding or bump") or extinguishing too late (an outer divot).
Jim Colt Hypertherm
As far as hole issues....each cnc machine has different backlash, different flex and different acceleration/speed capabilities based on design, condition and mass. I suggest trying a few different hole lead in configurations as well as lead out configurations to determine what works best for your machine.
Lead ins: start dead center in holes and try straight (90 degree) lead ins. These work best with machines with extremely good acceleration and zero backlash. Curved or tangential lead ins that slowly merge into the hole radius work best on machines with sluggish acceleration and / or backlash. The plasma arc moves around less when it approaches a 90 degree lead in.....has trouble and wiggles a bit when merging with a radial lead in!
Lead outs. More complex high definition class plasma cutters use an overburn that goes a calculated distance (staying on the hole radius) past the lead in kerf......yet shuts the plasma arc off before getting to the lead in kerf. Air (or oxygen) plasma does not instantly extinguish....so the CAM software on more complex systems uses its data files to time the shutoff of the arc (based on power level, material thickness and hole diameter) to eliminate the divot caused by the arc extinguishing too soon (an inner "ding or bump") or extinguishing too late (an outer divot).
Jim Colt Hypertherm
davek0974 wrote:Following on from the tips given in another thread on 12mm (thanks SeanP) I cut my first parts in 12mm tonight, learnt a few things too.
The settings ended up at...
45A
120v
1.3mm kerf
1.2s pierce delay
510mm/min speed
4mm pierce height
1.5mm cut height
Front and back of the parts... Edge detail in the notches... The notches exhibited the usual tail lag in the bottom corners, is there anything that can help this?
The tops of the notches were squared up by using loops on the path, this however caused me to waste a chunk on the first trial when the two loops touched and made the bit in the middle drop out - when the torch reached the 2nd loop it was cutting in air and turned itself off. I realised the error and altered the file for smaller loops that did not touch, this fixed it nicely but as it was running you could see the torch dive at each loop, just enough to touch the plate, not enough to cut the arc so i let it run. Maybe i'll turn the THC off on loops in future.
Minimal dross and it fell of easily, edge angularity was perfect, hole taper was acceptable, I still have issues with divots though, even on this thickness. Even though i gave a little overburn it still left a little tag at the bottom of the exit path.
Overall, I am mightily impressed, this came out better than my 3mm stuff, wouldn't mind doing more when i can.
-
- 4 Star Member
- Posts: 764
- Joined: Wed Aug 13, 2014 8:30 am
- Location: Hertfordshire, England
- Contact:
Re: First 12mm cuts tonight...
Thanks Jim,
TBH I had not thought of reducing acceleration, I have always been advised to go more, more, more but less does sound like a good idea there.
I can do an ove-burn but it didn't make much difference on the 3mm stuff maybe it will on the thicker, will try again.
I always use a perpendicular lead-in, I find it gives the best overall effect.
My issues are with the lead-out, always.
Come to think of it, maybe the other issue I am having is also related to too much acceleration - there is a little tag that remains at the end of the cuts, can't seem to shift it, maybe its created by the same lag i had in the notches but at the perp lead-in which is effectively a 90deg internal corner.
I have my machine tuned as high as it will go almost, I think its time to see what happens when de-tuned, I have been noticing a fair bit of slat wobble on some of my arty stuff where there is a 'rough' design - the table shakes quite violently at times. If I had made a note of the date, I have a feeling some of these issues started when I last tuned her up.
Next gap I get I will investigate.
What sort of acceleration figures are you guys seeing (Mach3) I know it's all relative but just a comparison.
TBH I had not thought of reducing acceleration, I have always been advised to go more, more, more but less does sound like a good idea there.
I can do an ove-burn but it didn't make much difference on the 3mm stuff maybe it will on the thicker, will try again.
I always use a perpendicular lead-in, I find it gives the best overall effect.
My issues are with the lead-out, always.
Come to think of it, maybe the other issue I am having is also related to too much acceleration - there is a little tag that remains at the end of the cuts, can't seem to shift it, maybe its created by the same lag i had in the notches but at the perp lead-in which is effectively a 90deg internal corner.
I have my machine tuned as high as it will go almost, I think its time to see what happens when de-tuned, I have been noticing a fair bit of slat wobble on some of my arty stuff where there is a 'rough' design - the table shakes quite violently at times. If I had made a note of the date, I have a feeling some of these issues started when I last tuned her up.
Next gap I get I will investigate.
What sort of acceleration figures are you guys seeing (Mach3) I know it's all relative but just a comparison.
-
- 3.5 Star Member
- Posts: 511
- Joined: Wed Apr 23, 2014 2:48 pm
Re: First 12mm cuts tonight...
40 inches per second per second normal for me, but I went to 20 down to 10 on .500 I was cutting.. I think 20 is not too bad overall..
I did not see any need to loop any outside corners in the little notched test piece I did.. Certainly not at 65 amps.. Might if you slow the accel down too much.. Worked well, and a Nitto air file. cleaned up the parts fast enough..
I think air plasma (every brand too) should have one of those, and a good belt sander.. Gets things about as good as it's going to get..
Black one in the middle. Just a nice tool to own for this stuff..
I did not see any need to loop any outside corners in the little notched test piece I did.. Certainly not at 65 amps.. Might if you slow the accel down too much.. Worked well, and a Nitto air file. cleaned up the parts fast enough..
I think air plasma (every brand too) should have one of those, and a good belt sander.. Gets things about as good as it's going to get..
Black one in the middle. Just a nice tool to own for this stuff..
- Attachments
-
- air tool porn..jpg (182.16 KiB) Viewed 1658 times
- air tool porn..jpg (182.16 KiB) Viewed 1658 times
-
- 4 Star Member
- Posts: 764
- Joined: Wed Aug 13, 2014 8:30 am
- Location: Hertfordshire, England
- Contact:
Re: First 12mm cuts tonight...
40inches/s/s is about 1016mm/s/s and I turned my one DOWN last night to 1500m/s/s 
Think I might go down again
Anyone else care to throw their figures in to the mix

Think I might go down again

Anyone else care to throw their figures in to the mix
