So many cutting issues. Going to pull my hair out
-
- 4 Star Member
- Posts: 950
- Joined: Thu Jan 02, 2014 6:33 pm
So many cutting issues. Going to pull my hair out
Machine is a torchmate 2x2 with machine torch (no height control) with Longevity 62i plasma cutter.
Had some cutting issues today that were driving me nuts. Had to cut out 16 guests out of 1/4" mild steel. I did line tests and had to cut out about 45-50 to get the 16 I needed. I don't even know where to begin with the issues. Realized the 2 stage dryer desiccant filter was pink and the junk regulator on the compressor kept changing. So I figured I would try and get a base line and put in a inline desiccant filter, and better regulator and new 3/8" hose.
Tried cutting 1/4" steel from from anywhere from 70 to 100psi. Tried from .70 up to .125" cut height. 35-40 amps. 35 amps won't cut 1/4" steel whatsoever unless it's 10 or 20 IPM
Started with all new s45 consumables. Piercing delay was set to .65 and it wouldn't punch through the 1/4" steel. I also drained the tank prior to doing all this. In making the 40 gussets or so and a few line tests I killed the desiccant dryers completely. They turned completely pink. So I guess my first issue is what could cause me to soooooo much moisture that it is killing my dryers within minutes of cutting?
I used metal coupon and put it between the tip and metal to gauge my cut height.
Is too much air pressure an issue? I think last week at 90psi it wouldn't punch through 1/8" and dropped it to 70psi and cut fine, but I don't know if the old regulator was to blame or what.
1) what could cause all the moisture issues?
2) is too much pressure a problem?
3) with more amperage do you need more pressure?
4) should thicker material have higher pierce/cut height?
this is the compressor, not that it should really matter as it's been great for the past year
http://www.harborfreight.com/29-gal-2-h ... 68127.html
s45 legit trafimet consumables 0.8 tip
And no matter the amperage it wouldn't cut the 1/4" steel at anything under 30IPM (as high as 40amps)
I have this customer that wants a bunch of parts and after today lol I would have been better off cutting them all from hand.
Had some cutting issues today that were driving me nuts. Had to cut out 16 guests out of 1/4" mild steel. I did line tests and had to cut out about 45-50 to get the 16 I needed. I don't even know where to begin with the issues. Realized the 2 stage dryer desiccant filter was pink and the junk regulator on the compressor kept changing. So I figured I would try and get a base line and put in a inline desiccant filter, and better regulator and new 3/8" hose.
Tried cutting 1/4" steel from from anywhere from 70 to 100psi. Tried from .70 up to .125" cut height. 35-40 amps. 35 amps won't cut 1/4" steel whatsoever unless it's 10 or 20 IPM
Started with all new s45 consumables. Piercing delay was set to .65 and it wouldn't punch through the 1/4" steel. I also drained the tank prior to doing all this. In making the 40 gussets or so and a few line tests I killed the desiccant dryers completely. They turned completely pink. So I guess my first issue is what could cause me to soooooo much moisture that it is killing my dryers within minutes of cutting?
I used metal coupon and put it between the tip and metal to gauge my cut height.
Is too much air pressure an issue? I think last week at 90psi it wouldn't punch through 1/8" and dropped it to 70psi and cut fine, but I don't know if the old regulator was to blame or what.
1) what could cause all the moisture issues?
2) is too much pressure a problem?
3) with more amperage do you need more pressure?
4) should thicker material have higher pierce/cut height?
this is the compressor, not that it should really matter as it's been great for the past year
http://www.harborfreight.com/29-gal-2-h ... 68127.html
s45 legit trafimet consumables 0.8 tip
And no matter the amperage it wouldn't cut the 1/4" steel at anything under 30IPM (as high as 40amps)
I have this customer that wants a bunch of parts and after today lol I would have been better off cutting them all from hand.
Torchmate 2x2 - Flashcut
Powermax 45 - Machine torch
Taig CNC Mill - Flashcut
Razorweld Distributor
Powermax 45 - Machine torch
Taig CNC Mill - Flashcut
Razorweld Distributor
-
- 3 Star Member
- Posts: 307
- Joined: Fri Dec 21, 2012 5:21 pm
Re: So many cutting issues. Going to pull my hair out
I don't recognize your machine but I don't cut anything over 10 Guage under 65 amp. It sounds like you have an under powered machine.
-
- 1.5 Star Member
- Posts: 34
- Joined: Tue Jul 09, 2013 1:04 pm
Re: So many cutting issues. Going to pull my hair out
I cut 1/4" quite often. I use 45A with the 45A consumables on my Hypertherm Powermax 65 at 48ipm, .15" pierce, .06" cut height.
But I also run 2 coalescing filters and a dedicated refrigerated drier for my plasma and have an 80gal, 3cyl, 2-stage Curtis Compressor.
Moisture/oil/contaminants will destroy your cuts no matter what kind of plasma or compressor you run. You must get the air dry and clean.
Moisture can be caused by a myriad of things;
Ambient temperature and humidity
How often your compressor cycles
How hot your compressor runs (more cycling makes it run hotter) cheaper pumps can run hotter
Type of airlines
Etc..
Yes, higher amperage takes more air pressure
Yes, Thicker material generally require a higher and longer pierce
Here's some 1/4" 4130 steel parts I cut for a fire axe project
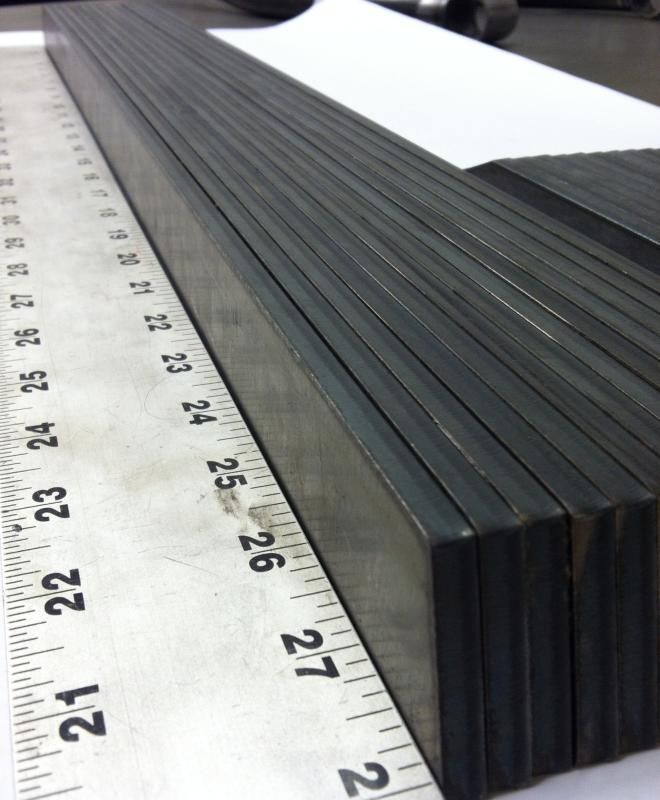
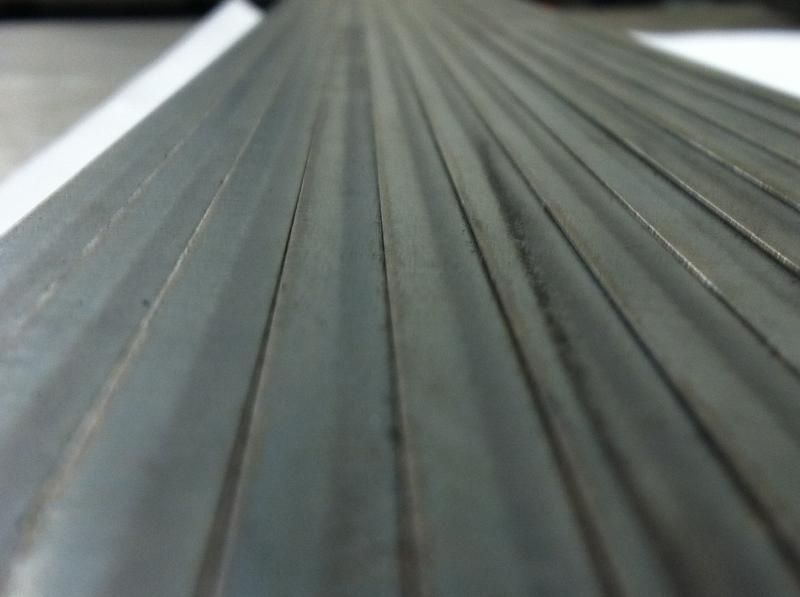
But I also run 2 coalescing filters and a dedicated refrigerated drier for my plasma and have an 80gal, 3cyl, 2-stage Curtis Compressor.
Moisture/oil/contaminants will destroy your cuts no matter what kind of plasma or compressor you run. You must get the air dry and clean.
Moisture can be caused by a myriad of things;
Ambient temperature and humidity
How often your compressor cycles
How hot your compressor runs (more cycling makes it run hotter) cheaper pumps can run hotter
Type of airlines
Etc..
Yes, higher amperage takes more air pressure
Yes, Thicker material generally require a higher and longer pierce
Here's some 1/4" 4130 steel parts I cut for a fire axe project
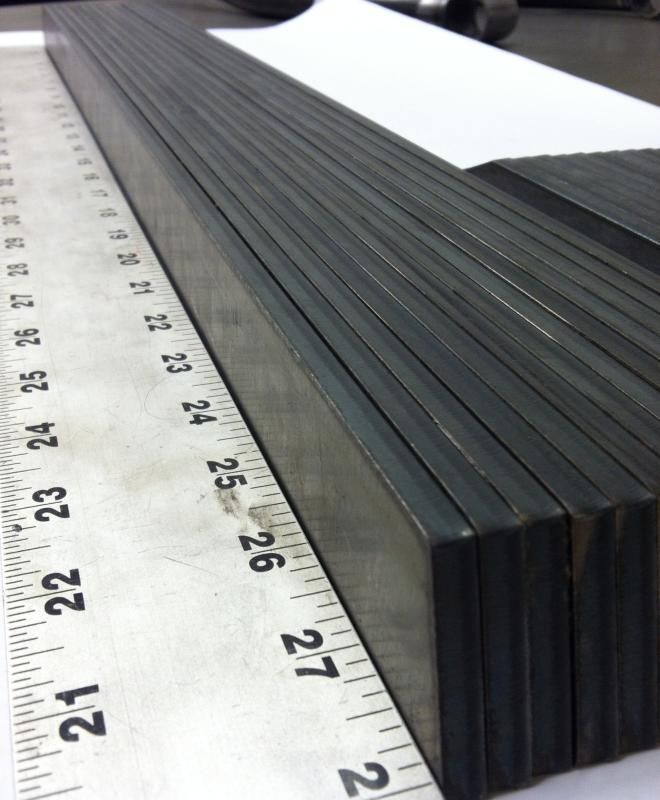
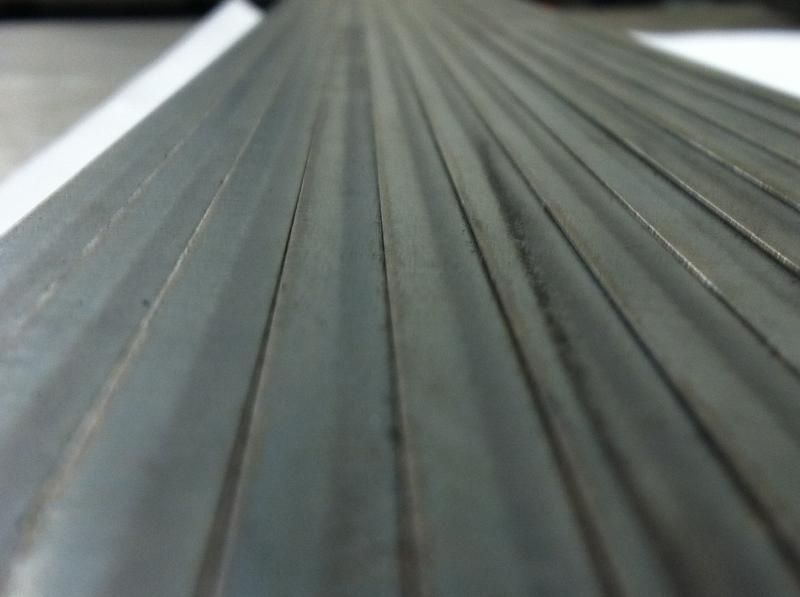
-
- 3.5 Star Member
- Posts: 511
- Joined: Wed Apr 23, 2014 2:48 pm
Re: So many cutting issues. Going to pull my hair out
I personally think it's time to get some clean air to try your cutter with.. If it has to come from a bottle then so be it. Then you will know if you need to totally ditch your Plasma cutter. Even my friends Hypertherm 85 was pretty dang hard on consumables, with a quality large filter. Finally got a Refrigerated to add to his setup, and consumable life/cut quality is excellent now. I have a few filters and a Deliquescent tower that keeps my air really dry. Same compressor as ZTFab has..My Esab Plasma is super with consumable life, and even the Lowly Cutmaster A-120 has proven to be great too. Sold on clean dry air/cool air.....first thing. then having enough flow also..
-
- 4 Star Member
- Posts: 950
- Joined: Thu Jan 02, 2014 6:33 pm
Re: So many cutting issues. Going to pull my hair out
I only have 1 220v 30 amp outlet so I am trying to stay with a 110v compressor and I think this is the largest I can go is what I have?
I have heard good things about the HF air dryer
http://m.harborfreight.com/compressed-a ... 40211.html
Should I try that or something else?
These desiccant filters used to last me a long time like 2 months or so.
I have heard good things about the HF air dryer
http://m.harborfreight.com/compressed-a ... 40211.html
Should I try that or something else?
These desiccant filters used to last me a long time like 2 months or so.
Torchmate 2x2 - Flashcut
Powermax 45 - Machine torch
Taig CNC Mill - Flashcut
Razorweld Distributor
Powermax 45 - Machine torch
Taig CNC Mill - Flashcut
Razorweld Distributor
- acourtjester
- 6 Star Elite Contributing Member
- Posts: 8169
- Joined: Sat Jun 02, 2012 6:04 pm
- Location: Pensacola, Fla
Re: So many cutting issues. Going to pull my hair out
There are things you need to check to find you problem.
The higher pressure you use the larger volume of air you use, is your compressor cycling a lot.
If you cut a small part does it cut well but as you cut larger parts (more parts) does the cut quality go down? This will show you compressor is not keeping up with air demands.
If the compressor is cycling a lot your air does not have time to cool and there for the moisture cannot drop out and this will cause the driers to go bad faster. If the compressor has a good CFM rating then the air storage is the problem you could add a large secondary tank and plumbing to increase the length travel of the air about 30 feet between tanks. Do put a drain drop after the first tank and the 30 feet of line. Search here for info about drying air and how to plumb the lines.
Are you attaching the work ground directly on to the metal you are cutting not on the table or slats of the table?
Another thing I think a 0.8mm tip is too small to cut ?? steel the Hypertherm manual shows the fine cut tips even using 45 amps are not rated to cut ?? steel.
Try doing an edge cut set at 0.060? at 45 amps larger tip (at least 0.9mm to 1.0mm) at 30 to 35 ipm and 80PSI. If it cuts well you are too high for cutting with 0.070?.
There a many using the same plasma unit and table you are so your problem is not there.
The higher pressure you use the larger volume of air you use, is your compressor cycling a lot.
If you cut a small part does it cut well but as you cut larger parts (more parts) does the cut quality go down? This will show you compressor is not keeping up with air demands.
If the compressor is cycling a lot your air does not have time to cool and there for the moisture cannot drop out and this will cause the driers to go bad faster. If the compressor has a good CFM rating then the air storage is the problem you could add a large secondary tank and plumbing to increase the length travel of the air about 30 feet between tanks. Do put a drain drop after the first tank and the 30 feet of line. Search here for info about drying air and how to plumb the lines.
Are you attaching the work ground directly on to the metal you are cutting not on the table or slats of the table?
Another thing I think a 0.8mm tip is too small to cut ?? steel the Hypertherm manual shows the fine cut tips even using 45 amps are not rated to cut ?? steel.
Try doing an edge cut set at 0.060? at 45 amps larger tip (at least 0.9mm to 1.0mm) at 30 to 35 ipm and 80PSI. If it cuts well you are too high for cutting with 0.070?.
There a many using the same plasma unit and table you are so your problem is not there.
DIY 4X4 Plasma/Router Table
Hypertherm PM65 Machine Torch
Drag Knife and Scribe
Miller Mig welder
13" metal lathe
Small Mill
Everlast PowerTig 255 EXT
Hypertherm PM65 Machine Torch
Drag Knife and Scribe
Miller Mig welder
13" metal lathe
Small Mill
Everlast PowerTig 255 EXT
-
- 4 Star Member
- Posts: 950
- Joined: Thu Jan 02, 2014 6:33 pm
Re: So many cutting issues. Going to pull my hair out
Paul those cuts look amazing!
I am going to try a 0.9 tip and 75psi. Will report back.
The compressor cycles here and there but not terrible often. I will have to time it. So if I fill the compressor and let it sit full of pressure the air will cool and not have as much moisture?
Should I also open the petcock and let if sit open overnight?
I am going to try a 0.9 tip and 75psi. Will report back.
The compressor cycles here and there but not terrible often. I will have to time it. So if I fill the compressor and let it sit full of pressure the air will cool and not have as much moisture?
Should I also open the petcock and let if sit open overnight?
Torchmate 2x2 - Flashcut
Powermax 45 - Machine torch
Taig CNC Mill - Flashcut
Razorweld Distributor
Powermax 45 - Machine torch
Taig CNC Mill - Flashcut
Razorweld Distributor
- acourtjester
- 6 Star Elite Contributing Member
- Posts: 8169
- Joined: Sat Jun 02, 2012 6:04 pm
- Location: Pensacola, Fla
Re: So many cutting issues. Going to pull my hair out
my compressor is left on and full all the time you could put a ball valve in the output line and shut it at night is you like.
having a long line for the air to travel (30' ) will cool the air and the moisture will drop out but it needs to plumbed so the input is lower then the output so the water will drain back to the start. if you don't have the room you can fold the air line back and forth up the wall the air just needs to cool to drop the moisture.
check out this post
http://www.plasmaspider.com/viewtopic.p ... ure#p78263
and
http://www.plasmaspider.com/viewtopic.p ... ure#p77482
having a long line for the air to travel (30' ) will cool the air and the moisture will drop out but it needs to plumbed so the input is lower then the output so the water will drain back to the start. if you don't have the room you can fold the air line back and forth up the wall the air just needs to cool to drop the moisture.
check out this post
http://www.plasmaspider.com/viewtopic.p ... ure#p78263
and
http://www.plasmaspider.com/viewtopic.p ... ure#p77482
DIY 4X4 Plasma/Router Table
Hypertherm PM65 Machine Torch
Drag Knife and Scribe
Miller Mig welder
13" metal lathe
Small Mill
Everlast PowerTig 255 EXT
Hypertherm PM65 Machine Torch
Drag Knife and Scribe
Miller Mig welder
13" metal lathe
Small Mill
Everlast PowerTig 255 EXT
-
- 4 Star Member
- Posts: 950
- Joined: Thu Jan 02, 2014 6:33 pm
Re: So many cutting issues. Going to pull my hair out
Thanks, I will check out those links.
So tonight I figured i would try again. Found out the PT60 torch is rated for 65-75psi. So I ran the compressor to my 2 stage dryer to the plasma.
Cut height I used a piece of 14g material so .070.
new tip and electrode, 0.9 tip. Tried at 40 and 45 amps at 27IPM.
I did make a video that but that one cut ok the one before was crap. It started to cut well then turned and it wouldn't cut through the material. I find that happens more often than I like on thicker stuff. Say 3/4 of it cuts great and the rest doesn't punch through the material.
I tried 40, 45amps, 75 and 80psi air pressure, .070 and .100 cut heights.
Torch is pretty straight (with my el cheapo level) my really nice one is too large

These were the best hole cuts I got, the rest were terrible
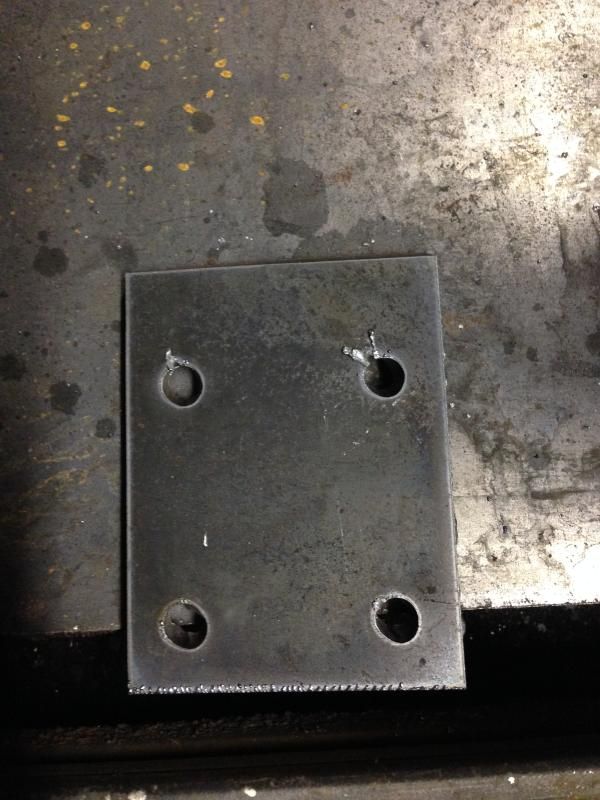
The angularity is ridiculous. Not sure why.
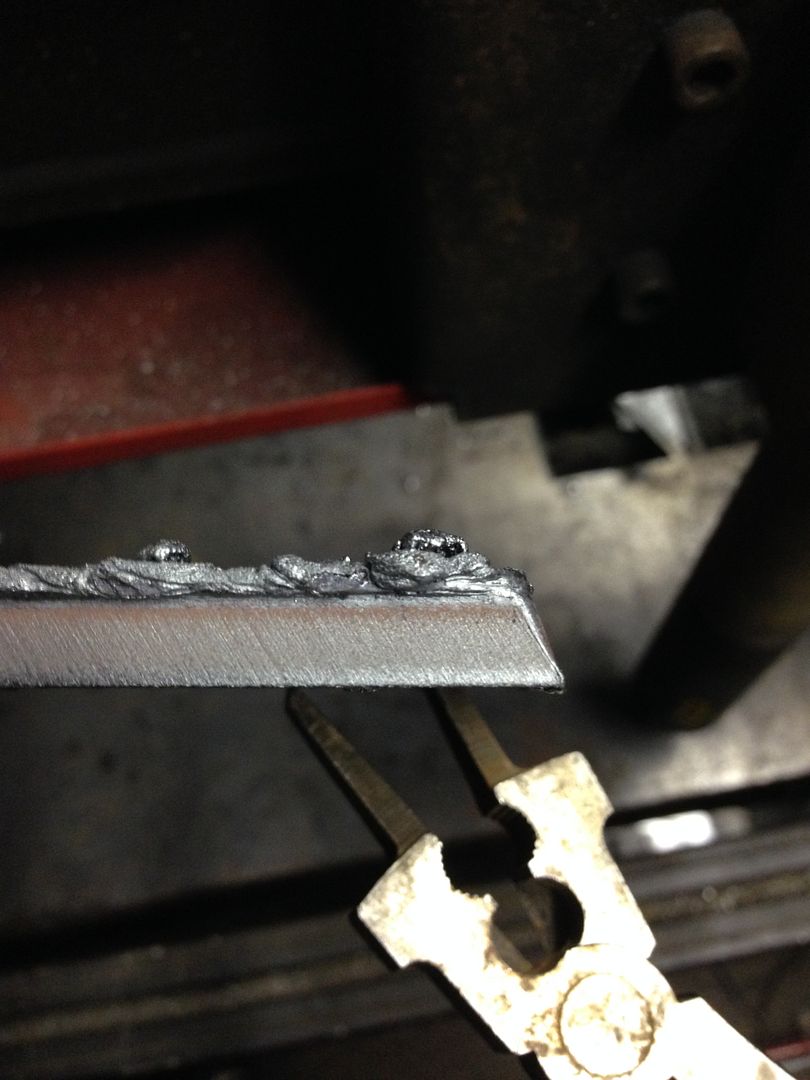
All these cuts were much better than last night but I still had to beat on the material with something to get them to break free, here is the back side
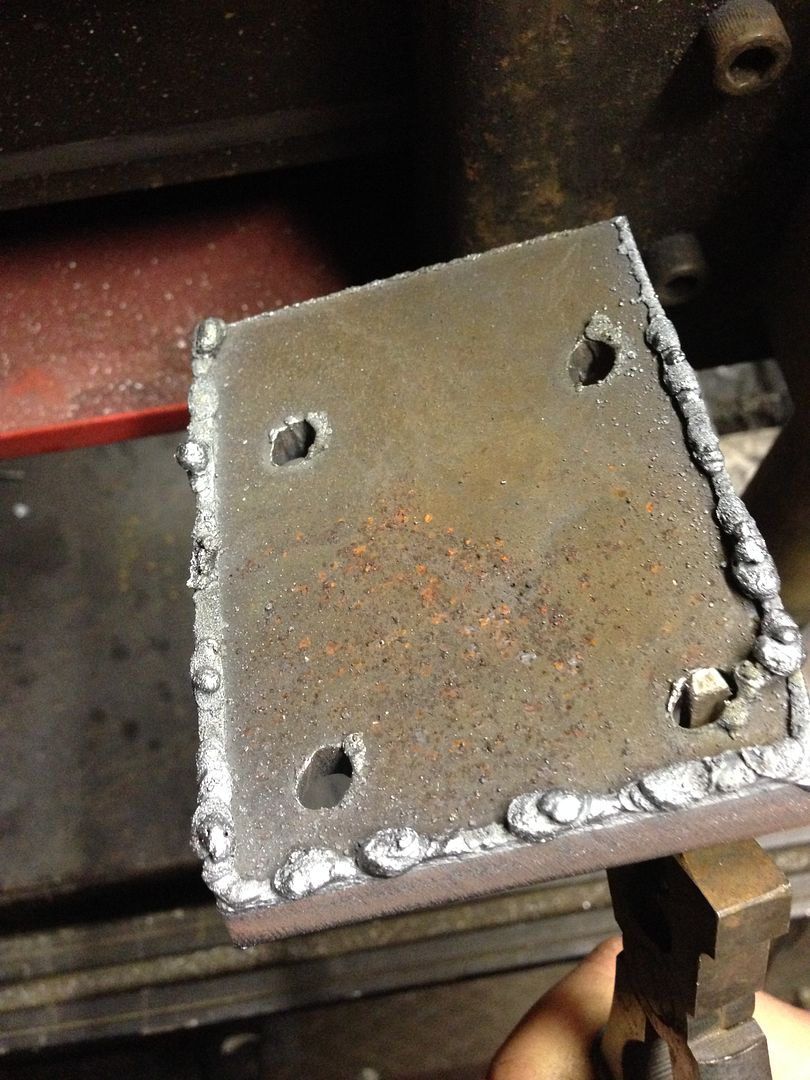
I timed the compressor, it fills up to 145psi and shuts off; it will cut for 1 minute and 20 seconds before it kicks back on. So I guess it does cycle pretty often.
I got this customer that needs a lot of parts cut and it's a reoccurring customer (or is supposed to be) and I'm on week 2 of getting him his stuff because of cutting issues. I cut probably 40 or 50 parts so far. Then I had to redrill each hole and grind each one. I'm probably 5 hours into his stuff already. I do see the advantage of getting better stuff and going from the table to the mailbox!
So tonight I figured i would try again. Found out the PT60 torch is rated for 65-75psi. So I ran the compressor to my 2 stage dryer to the plasma.
Cut height I used a piece of 14g material so .070.
new tip and electrode, 0.9 tip. Tried at 40 and 45 amps at 27IPM.
I did make a video that but that one cut ok the one before was crap. It started to cut well then turned and it wouldn't cut through the material. I find that happens more often than I like on thicker stuff. Say 3/4 of it cuts great and the rest doesn't punch through the material.
I tried 40, 45amps, 75 and 80psi air pressure, .070 and .100 cut heights.
Torch is pretty straight (with my el cheapo level) my really nice one is too large

These were the best hole cuts I got, the rest were terrible
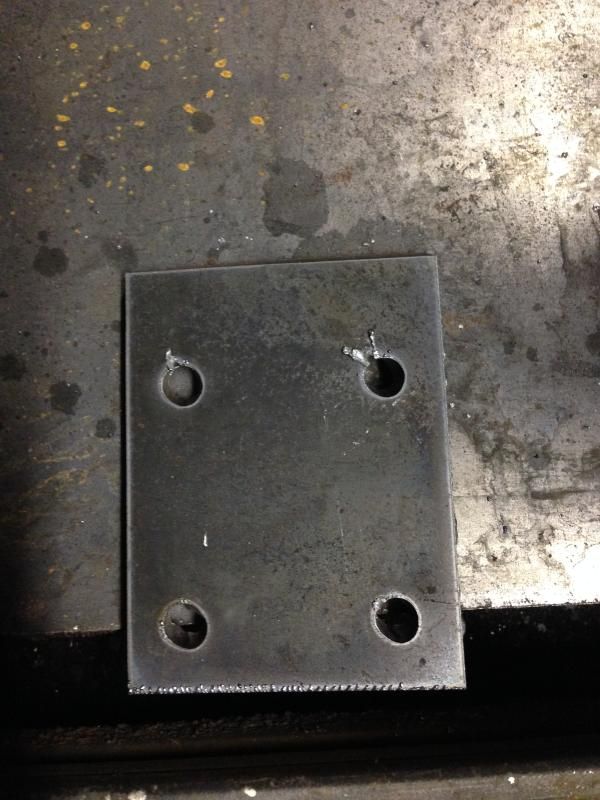
The angularity is ridiculous. Not sure why.
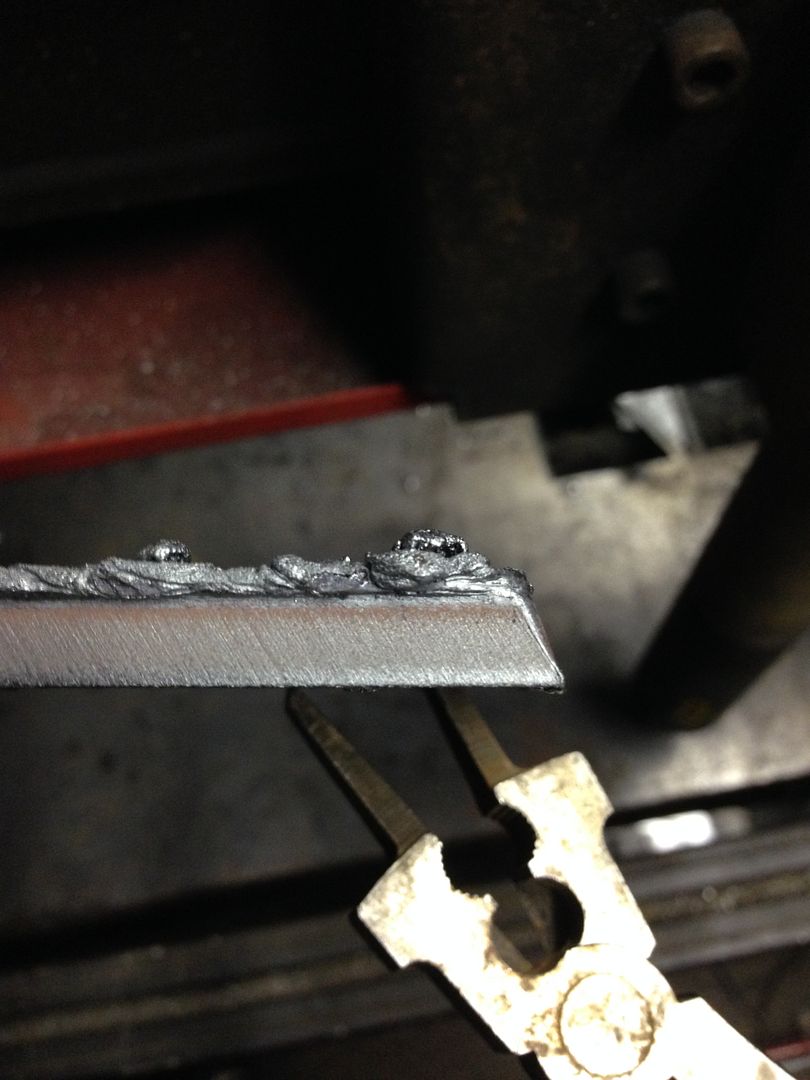
All these cuts were much better than last night but I still had to beat on the material with something to get them to break free, here is the back side
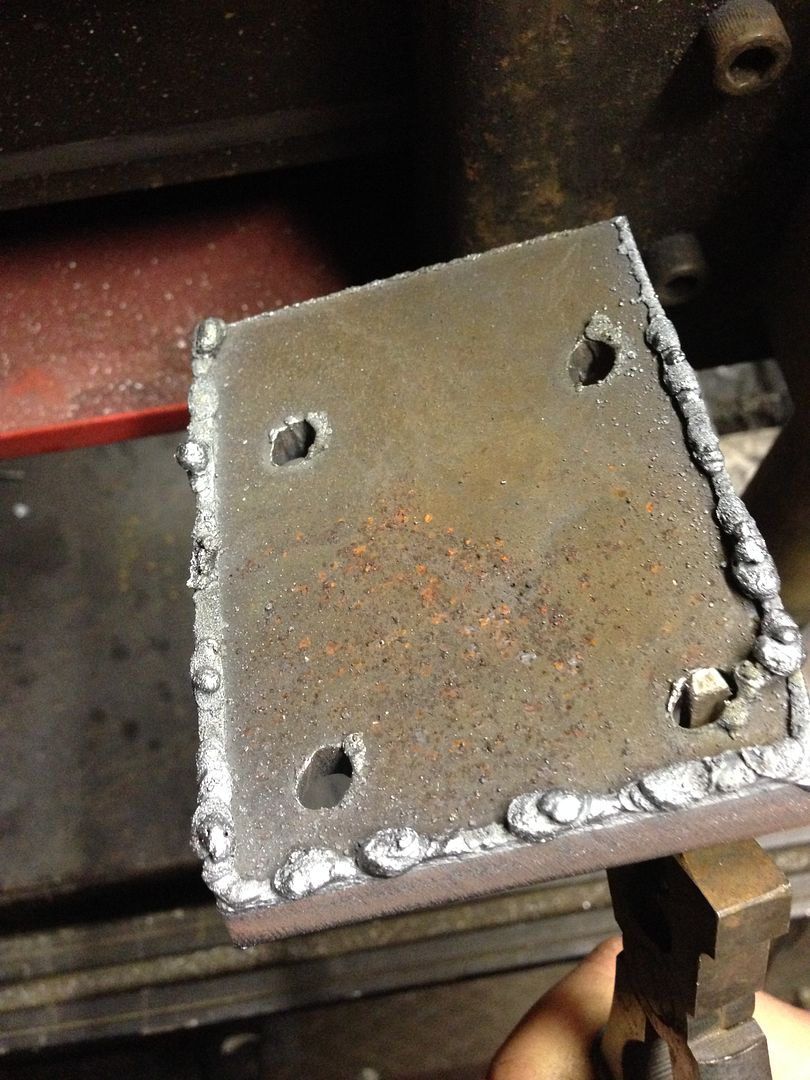
I timed the compressor, it fills up to 145psi and shuts off; it will cut for 1 minute and 20 seconds before it kicks back on. So I guess it does cycle pretty often.
I got this customer that needs a lot of parts cut and it's a reoccurring customer (or is supposed to be) and I'm on week 2 of getting him his stuff because of cutting issues. I cut probably 40 or 50 parts so far. Then I had to redrill each hole and grind each one. I'm probably 5 hours into his stuff already. I do see the advantage of getting better stuff and going from the table to the mailbox!
Torchmate 2x2 - Flashcut
Powermax 45 - Machine torch
Taig CNC Mill - Flashcut
Razorweld Distributor
Powermax 45 - Machine torch
Taig CNC Mill - Flashcut
Razorweld Distributor
- acourtjester
- 6 Star Elite Contributing Member
- Posts: 8169
- Joined: Sat Jun 02, 2012 6:04 pm
- Location: Pensacola, Fla
Re: So many cutting issues. Going to pull my hair out
That is bad
Are your cuts all with that angle on all 4 sides or just 2 like right and left but front and back OK???
if you have 2 sides OK and 2 with angles your torch is not straight I see you checked one direction. Do you have a swirl ring have you checked it. I had a problem with a torch's retaining ring I could not see any thing wrong but after changing it the torch cut straight again. From what you are saying something changed in the past you cut good now bad.
Are your cuts all with that angle on all 4 sides or just 2 like right and left but front and back OK???
if you have 2 sides OK and 2 with angles your torch is not straight I see you checked one direction. Do you have a swirl ring have you checked it. I had a problem with a torch's retaining ring I could not see any thing wrong but after changing it the torch cut straight again. From what you are saying something changed in the past you cut good now bad.
- Attachments
-
- angle.jpg (8.34 KiB) Viewed 4597 times
- angle.jpg (8.34 KiB) Viewed 4597 times
DIY 4X4 Plasma/Router Table
Hypertherm PM65 Machine Torch
Drag Knife and Scribe
Miller Mig welder
13" metal lathe
Small Mill
Everlast PowerTig 255 EXT
Hypertherm PM65 Machine Torch
Drag Knife and Scribe
Miller Mig welder
13" metal lathe
Small Mill
Everlast PowerTig 255 EXT
-
- 4 Star Member
- Posts: 950
- Joined: Thu Jan 02, 2014 6:33 pm
Re: So many cutting issues. Going to pull my hair out
Swirl ring looks to be in good shape. Nothing noticeable, but I'll double check.
I grounded all the parts down last night, but I'll do another cut, I believe it was just the left and right side that were angled.
What else is odd (and maybe it's due to moisture?) Some of the cuts are great then in the middle of a cut it goes to crap and builds a lot of dross on the top and won't punch through.
I grounded all the parts down last night, but I'll do another cut, I believe it was just the left and right side that were angled.
What else is odd (and maybe it's due to moisture?) Some of the cuts are great then in the middle of a cut it goes to crap and builds a lot of dross on the top and won't punch through.
Torchmate 2x2 - Flashcut
Powermax 45 - Machine torch
Taig CNC Mill - Flashcut
Razorweld Distributor
Powermax 45 - Machine torch
Taig CNC Mill - Flashcut
Razorweld Distributor
-
- 4 Star Member
- Posts: 950
- Joined: Thu Jan 02, 2014 6:33 pm
Re: So many cutting issues. Going to pull my hair out
Torchmate 2x2 - Flashcut
Powermax 45 - Machine torch
Taig CNC Mill - Flashcut
Razorweld Distributor
Powermax 45 - Machine torch
Taig CNC Mill - Flashcut
Razorweld Distributor
-
- 4 Star Member
- Posts: 764
- Joined: Wed Aug 13, 2014 8:30 am
- Location: Hertfordshire, England
- Contact:
Re: So many cutting issues. Going to pull my hair out
gamble wrote:Swirl ring looks to be in good shape. Nothing noticeable, but I'll double check.
I grounded all the parts down last night, but I'll do another cut, I believe it was just the left and right side that were angled.
What else is odd (and maybe it's due to moisture?) Some of the cuts are great then in the middle of a cut it goes to crap and builds a lot of dross on the top and won't punch through.
When I had moisture In my system, it made the arc go out then reignite almost immediately, i fitted a refrigerated dryer and it stopped doing it.
I get that angularity when I've blown a tip - straight on two sides and angled on two.
-
- 3.5 Star Member
- Posts: 563
- Joined: Fri Jan 24, 2014 11:03 pm
Re: So many cutting issues. Going to pull my hair out
1. You have a moisture problem, I have the harbor freight refr. air dryer, works fine. I wasn't aware at the time but there is a company that makes them in the usa that advertises on this site at the top. Maybe someone can recall the name.
2. Are you grounding directly to the sheet or just the slats back to the machine? Need to be grounded directly from the work back to machine.
3. You have a moisture problem.
4. You need a hypertherm.
5. You have a moisture problem.
6. You need a hypertherm.
Shane
2. Are you grounding directly to the sheet or just the slats back to the machine? Need to be grounded directly from the work back to machine.
3. You have a moisture problem.
4. You need a hypertherm.
5. You have a moisture problem.
6. You need a hypertherm.
Shane
- CNCCAJUN
- 4 Star Member
- Posts: 1108
- Joined: Mon Dec 26, 2011 11:38 pm
- Location: Baton Rouge, LA
Re: So many cutting issues. Going to pull my hair out
MacAir
Got one . . . works great . . .forget to turn it on & cuts look like crap . . .
Steve
Got one . . . works great . . .forget to turn it on & cuts look like crap . . .
Steve
Smiling Gator Metal Works, LLC
Dynatorch 4X4 XLS
PowerMAX 85
Baton Rouge, Louisiana
Dynatorch 4X4 XLS
PowerMAX 85
Baton Rouge, Louisiana
- tnbndr
- 4.5 Star Elite Contributing Member
- Posts: 1690
- Joined: Mon Jan 09, 2012 4:30 pm
- Location: New Berlin, WI
- Contact:
Re: So many cutting issues. Going to pull my hair out
MACAIR, I have one also and it works great for under $800 bucks and made in the USA.
That flare out on the lettering looks like a lead out but could be moisture also.
You have a moisture problem or your air pressure is running low when it stops cutting through.
That flare out on the lettering looks like a lead out but could be moisture also.
You have a moisture problem or your air pressure is running low when it stops cutting through.
Dennis
LDR 4x8, Scribe, DTHCIV
Hypertherm PM45, Macair Dryer
DeVilbiss Air America 6.5HP, 80Gal., 175psi, Two Stage
16.9scfm@100psi, 16.0scfm@175psi
Miller 215 MultiMatic
RW 390E Slip Roll (Powered)
AutoCAD, SheetCAM, Mach 3
http://ikescreations.com
LDR 4x8, Scribe, DTHCIV
Hypertherm PM45, Macair Dryer
DeVilbiss Air America 6.5HP, 80Gal., 175psi, Two Stage
16.9scfm@100psi, 16.0scfm@175psi
Miller 215 MultiMatic
RW 390E Slip Roll (Powered)
AutoCAD, SheetCAM, Mach 3
http://ikescreations.com
- modelaratrod
- 2 Star Member
- Posts: 86
- Joined: Tue Jul 23, 2013 12:41 pm
- Location: Colorado
Re: So many cutting issues. Going to pull my hair out
If your desiccant is changing that fast you have a lot of moisture. Drain the tank & cook the desiccant until it's blue again and try it again. I had tons of misfires and wonky cuts with my PM85 until I finished my air system. I would say a refrigerated air dryer is a must along with desiccant & coalescing filters. I also run a motor guard filter, the one that looks like a toilet paper roll inside. And it's been smooth sailing every since, and I can't remember when I changed out the consumables on the torch last. 

5x10 Torchmate 2 w/AVHC
Hypertherm PM85 w/ machine & hand torch.
Hypertherm PM85 w/ machine & hand torch.
-
- 4 Star Member
- Posts: 950
- Joined: Thu Jan 02, 2014 6:33 pm
Re: So many cutting issues. Going to pull my hair out
Was cutting some 14g steel tonight with a very very close torch height. 38amps and 120IPM, cut very well, but a few spots didn't punch through. It was all going very well then just stops cutting through the metal then a few seconds later it's back to cutting through. So I ruined 2 pieces tonight because of that.
I'm assuming that's moisture related?
I'm assuming that's moisture related?
Torchmate 2x2 - Flashcut
Powermax 45 - Machine torch
Taig CNC Mill - Flashcut
Razorweld Distributor
Powermax 45 - Machine torch
Taig CNC Mill - Flashcut
Razorweld Distributor
-
- 4 Star Member
- Posts: 764
- Joined: Wed Aug 13, 2014 8:30 am
- Location: Hertfordshire, England
- Contact:
Re: So many cutting issues. Going to pull my hair out
Did the torch go out then re-start?
If so then that is exactly the issue I had with moisture in my air.
I fitted a cheap(ish) refrigerated dryer (?450) from Abac ltd and she's been happy ever since.
If so then that is exactly the issue I had with moisture in my air.
I fitted a cheap(ish) refrigerated dryer (?450) from Abac ltd and she's been happy ever since.
- _Ogre
- 3.5 Star Member
- Posts: 529
- Joined: Sun Sep 15, 2013 4:26 pm
- Location: Motown
Re: So many cutting issues. Going to pull my hair out
it sounds like moisture is your first concern, fix that and other problems may be minor
before running out and buying a refrigerated air dryer, even those need cooled dry air in them or they get overloaded
i suspect your running a 3/8'' rubber hose from the compressor to the plasma table, not a good idea
buy 40 feet of 3/4'' copper tube and a fist full of 90*s to make up a one of these air cooler/dryer loops
1/2'' copper would probably work just as well with your compressor for less money, also less surface area
air in the top, slope all tubing to the bottom to a T, drip leg down to a valve and up with dry(er) air
if you block walls in your shop fasten your new air cooler/dryer to the block wall for a heat sink
it doesn't have to be just like the pic, it's just a pic i downloaded. maybe 20 ft of copper in this
shorten the drops, 90* down, street el 90* back (or short nipple and 90* back) and just as wide as you can get it
make it look like this
air in on top
l___________________________
___________________________l use shortest drops as possible
l___________________________
___________________________l
l___________________________
___________________________l make it a 3 feet wide or wider
l___________________________
___________________________l
l air out up
l
l
l drain valve at bottom of drip leg
if that^^^ makes any sense
even if you buy a refrigerated air dry this will cool and dry the air feeding into the dryer
you should be able to get rid of the desiccant in your system, save the desiccant for spraying paint
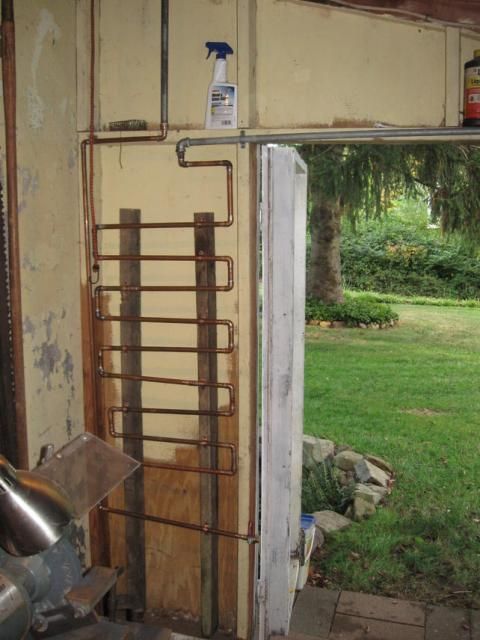
this is our setup in a commercial shop with plasma table, 3 techs, 3 lifts, painter and paint booth
we have 60 feet of 1'' steel line before any air distribution
yes we use desiccant at the paint booth it lasts 3 months before we change the desiccant
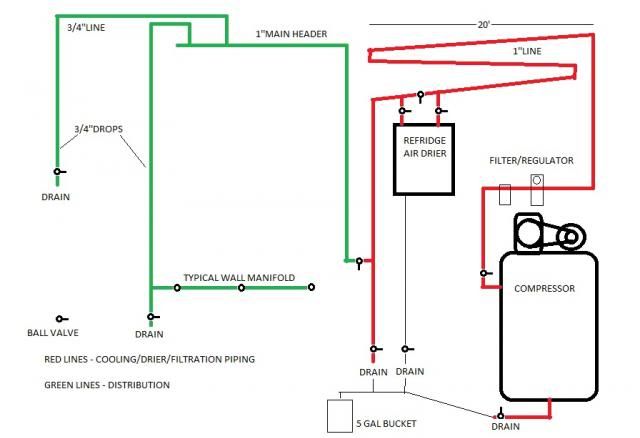
before running out and buying a refrigerated air dryer, even those need cooled dry air in them or they get overloaded
i suspect your running a 3/8'' rubber hose from the compressor to the plasma table, not a good idea
buy 40 feet of 3/4'' copper tube and a fist full of 90*s to make up a one of these air cooler/dryer loops
1/2'' copper would probably work just as well with your compressor for less money, also less surface area
air in the top, slope all tubing to the bottom to a T, drip leg down to a valve and up with dry(er) air
if you block walls in your shop fasten your new air cooler/dryer to the block wall for a heat sink
it doesn't have to be just like the pic, it's just a pic i downloaded. maybe 20 ft of copper in this
shorten the drops, 90* down, street el 90* back (or short nipple and 90* back) and just as wide as you can get it
make it look like this
air in on top
l___________________________
___________________________l use shortest drops as possible
l___________________________
___________________________l
l___________________________
___________________________l make it a 3 feet wide or wider
l___________________________
___________________________l
l air out up
l
l
l drain valve at bottom of drip leg
if that^^^ makes any sense

even if you buy a refrigerated air dry this will cool and dry the air feeding into the dryer
you should be able to get rid of the desiccant in your system, save the desiccant for spraying paint
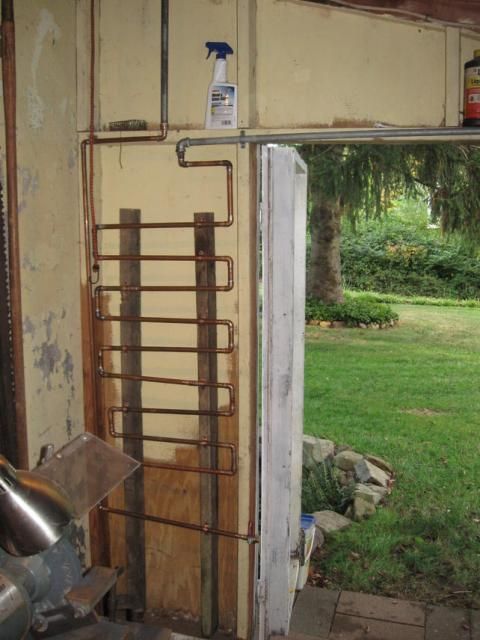
this is our setup in a commercial shop with plasma table, 3 techs, 3 lifts, painter and paint booth
we have 60 feet of 1'' steel line before any air distribution
yes we use desiccant at the paint booth it lasts 3 months before we change the desiccant
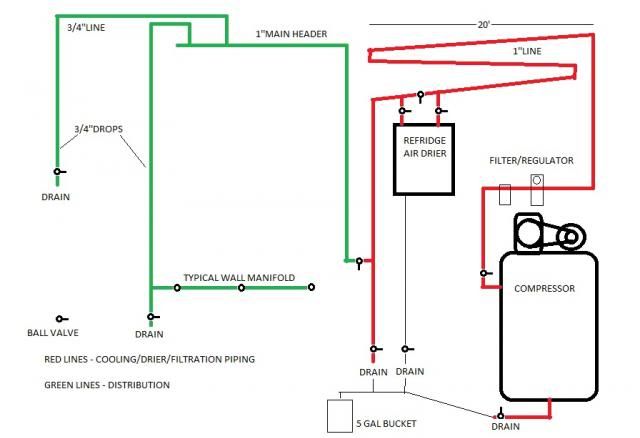
-
- 4 Star Member
- Posts: 950
- Joined: Thu Jan 02, 2014 6:33 pm
Re: So many cutting issues. Going to pull my hair out
I may try that.
What's wrong with 3/8" hose?
What's wrong with 3/8" hose?
Torchmate 2x2 - Flashcut
Powermax 45 - Machine torch
Taig CNC Mill - Flashcut
Razorweld Distributor
Powermax 45 - Machine torch
Taig CNC Mill - Flashcut
Razorweld Distributor
-
- 4 Star Member
- Posts: 950
- Joined: Thu Jan 02, 2014 6:33 pm
Re: So many cutting issues. Going to pull my hair out
Before I try that would I be better off buying that air drier from harbor freight?
Anyone know what the amp draw on it is?
If thata the better option I may just do that and not have to worry about mosture issues.
It's $370 shipped after tax, shipping and 20% off.
Anyone know what the amp draw on it is?
If thata the better option I may just do that and not have to worry about mosture issues.
It's $370 shipped after tax, shipping and 20% off.
Torchmate 2x2 - Flashcut
Powermax 45 - Machine torch
Taig CNC Mill - Flashcut
Razorweld Distributor
Powermax 45 - Machine torch
Taig CNC Mill - Flashcut
Razorweld Distributor
- _Ogre
- 3.5 Star Member
- Posts: 529
- Joined: Sun Sep 15, 2013 4:26 pm
- Location: Motown
Re: So many cutting issues. Going to pull my hair out
nothing wrong with rubber hose, but i have a feeling that's the only line between your tank and plasma cutter
rubber hose won't dissipate much heat or separate much water out, plus any water that does condense goes right into the plasma cutter
your compressor gets quite hot, you need to cool the air in the lines to get the moisture to condense and drop out
right now, your cooling the air and condensing the water out, inside the plasma cutter and in the swirl ring
the static copper air cooler will probably cool the air sufficient enough to get dry air
just be sure to drain into a drip leg sufficient enough to gather the water
i would try the static air cooler/dryer before i bought a refrigerated dryer
40 ft of 1/2'' copper pipe and 20 90* bends will set you back $40
rubber hose won't dissipate much heat or separate much water out, plus any water that does condense goes right into the plasma cutter
your compressor gets quite hot, you need to cool the air in the lines to get the moisture to condense and drop out
right now, your cooling the air and condensing the water out, inside the plasma cutter and in the swirl ring
the static copper air cooler will probably cool the air sufficient enough to get dry air
just be sure to drain into a drip leg sufficient enough to gather the water
i would try the static air cooler/dryer before i bought a refrigerated dryer
40 ft of 1/2'' copper pipe and 20 90* bends will set you back $40
bulltear 4x8 cnc plasma table, candcnc bladerunner w/dthc, hypertherm powermax 65, sheetcam, mach3
laser cross hair for hypertherm torch http://www.plasmaspider.com/viewtopic.php?f=6&t=12508
an ogre smiley
how cool!
laser cross hair for hypertherm torch http://www.plasmaspider.com/viewtopic.php?f=6&t=12508
an ogre smiley

-
- 4 Star Member
- Posts: 950
- Joined: Thu Jan 02, 2014 6:33 pm
Re: So many cutting issues. Going to pull my hair out
Borrowing a PM45 right now. did some cuts yesterday and got sick so haven't had time to play with it. Going to hopefully get some done tonight. No fine cut consumables
just standard shielded stuff. Tried per the book specs of .15 delay time for 14g material. I believe the book specs are good but the delay from the signal controller box. I had noticed that on my other cutter as well. Had to up to .4 or .5. But it cuts well and FAST. Up to 280IPM.
I got a lot of dross still.
14g, 45amps, from 150 up to 280 IPM. Cut height I tried .3 up to .5 (roughly) just using scrap to gauge the distance.
What's MOST impressive is the fact that the hypertherm air filter on the back and the compressor running while cutting didn't seem to affect it whatsoever. I may in fact just scrap the air dryer idea and get the hyperthem filter only (if it's reusable)
Maybe pair that with a motorguard too.
Hopefully my back is good enough to lift some 1/4" plate up and see how well that cuts.
One thing I did notice that others may or may not notice is how cool the part is after cutting. I cut a small name tag and it was hot but I could still hold it. I'm pretty sure with my other machine it was too hot to hold in general, but I'll double check. I have to give this thing back in a week and I already don't want to
I'll be sure to do some cuts on this and then on mine with the same settings and show pics.
Oh one other thing. The machine torch holder from torchmate doesn't fit well with the hypertherm at all. it was a huge struggle to get it into the torch holder then the knob to turn the height up/down just kept stripping and wouldn't grab the gear on the machine torch. Keep in mind I've NEVER used it before, since my machine torch doesn't have the gear track. So a little disappointed that the torch holder that costs $200 is crappy. I even wanted to add the gear to my machine torch but I guess I won't be doing that now.

I got a lot of dross still.
14g, 45amps, from 150 up to 280 IPM. Cut height I tried .3 up to .5 (roughly) just using scrap to gauge the distance.
What's MOST impressive is the fact that the hypertherm air filter on the back and the compressor running while cutting didn't seem to affect it whatsoever. I may in fact just scrap the air dryer idea and get the hyperthem filter only (if it's reusable)
Maybe pair that with a motorguard too.
Hopefully my back is good enough to lift some 1/4" plate up and see how well that cuts.
One thing I did notice that others may or may not notice is how cool the part is after cutting. I cut a small name tag and it was hot but I could still hold it. I'm pretty sure with my other machine it was too hot to hold in general, but I'll double check. I have to give this thing back in a week and I already don't want to

I'll be sure to do some cuts on this and then on mine with the same settings and show pics.
Oh one other thing. The machine torch holder from torchmate doesn't fit well with the hypertherm at all. it was a huge struggle to get it into the torch holder then the knob to turn the height up/down just kept stripping and wouldn't grab the gear on the machine torch. Keep in mind I've NEVER used it before, since my machine torch doesn't have the gear track. So a little disappointed that the torch holder that costs $200 is crappy. I even wanted to add the gear to my machine torch but I guess I won't be doing that now.
Torchmate 2x2 - Flashcut
Powermax 45 - Machine torch
Taig CNC Mill - Flashcut
Razorweld Distributor
Powermax 45 - Machine torch
Taig CNC Mill - Flashcut
Razorweld Distributor
-
- 4 Star Member
- Posts: 764
- Joined: Wed Aug 13, 2014 8:30 am
- Location: Hertfordshire, England
- Contact:
Re: So many cutting issues. Going to pull my hair out
Your cut height seems wrong - 0.3-0.5????
Should be 0.06 cut and 0.15 pierce in the book?
A cut of 0.5 would surely give dross?
Should be 0.06 cut and 0.15 pierce in the book?
A cut of 0.5 would surely give dross?