Torchmate X 5x10 - Hypotherm PM85 - .750 plate ... what should i expect?
-
- 1 Star Member
- Posts: 13
- Joined: Wed Jun 17, 2015 9:53 am
Torchmate X 5x10 - Hypotherm PM85 - .750 plate ... what should i expect?
So, i just recently bought a "new" but used 5x10 X Series Torchmate table, its one year old, and has less then 30 min of operation time on it.
The package i purchased includes a Hypotherm Powermax 85 plasma cutter. Im going to be cutting a decent amount of .750 plate steel with this setup.... what kind of cut quality should i expect?
I know it will probably take time to get dialed in, but what kind of cut quality are people getting? I would love to see some photos of peoples cuts with this cutter.
Thanks !
The package i purchased includes a Hypotherm Powermax 85 plasma cutter. Im going to be cutting a decent amount of .750 plate steel with this setup.... what kind of cut quality should i expect?
I know it will probably take time to get dialed in, but what kind of cut quality are people getting? I would love to see some photos of peoples cuts with this cutter.
Thanks !
-
- 5 Star Elite Contributing Member
- Posts: 3087
- Joined: Mon Jul 20, 2009 11:18 pm
- Location: North Carolina
Re: Torchmate X 5x10 - Hypotherm PM85 - .750 plate ... what should i expect?
All cut with Powermax85 on a cnc machine (Plasmacam) at various power levels, book speeds and heights from the Hypertherm manual.
1st is 1/4" steel with expected hole dimensions, 2nd is 3/8" steel showing edge quality and squareness, 3rd is 1/2" plate with 1/2" dia holes, next is showing holes on 1/4". lifting lug is as cut 3/4".
The Torchmate can do similar cuts. They will never be waterjet quality, but will be faster, much lower cost and good enough for the majority of fabricating needs. Keep in mind that a waterjet that can cut 3/4" steel will cost in excess of $200k, the Torchmate and Powermax85 is under $30k. There are high definition plasma systems in the $100k range that will cut much closer to water jet and laser at a lower capital cost and much lower operating cost.
Jim Colt Hypertherm
]
1st is 1/4" steel with expected hole dimensions, 2nd is 3/8" steel showing edge quality and squareness, 3rd is 1/2" plate with 1/2" dia holes, next is showing holes on 1/4". lifting lug is as cut 3/4".
The Torchmate can do similar cuts. They will never be waterjet quality, but will be faster, much lower cost and good enough for the majority of fabricating needs. Keep in mind that a waterjet that can cut 3/4" steel will cost in excess of $200k, the Torchmate and Powermax85 is under $30k. There are high definition plasma systems in the $100k range that will cut much closer to water jet and laser at a lower capital cost and much lower operating cost.
Jim Colt Hypertherm
]
-
- 1 Star Member
- Posts: 13
- Joined: Wed Jun 17, 2015 9:53 am
Re: Torchmate X 5x10 - Hypotherm PM85 - .750 plate ... what should i expect?
at the price im getting this machine, its going to put me ahead of the game for sure.
Could you also help me out with another thing... I want to get an air compressor to dedicate to the table to run the plasma. What would you reccomend.
I think the water jet cost about 250k new, and its fantastic, but its often not needed.... which is what led me to find this plasma deal, and i just dont think i can go wrong with it. I really would like to be able to cut .750 plate, can you reccomend some settings to start with? or just go with the PM guide settings?
Could you also help me out with another thing... I want to get an air compressor to dedicate to the table to run the plasma. What would you reccomend.
I think the water jet cost about 250k new, and its fantastic, but its often not needed.... which is what led me to find this plasma deal, and i just dont think i can go wrong with it. I really would like to be able to cut .750 plate, can you reccomend some settings to start with? or just go with the PM guide settings?
-
- 3 Star Member
- Posts: 359
- Joined: Tue Oct 28, 2014 1:21 pm
Re: Torchmate X 5x10 - Hypotherm PM85 - .750 plate ... what should i expect?
So far for me, the PM cut specs have been spot on. I've only had my PM65 for a short time but I'd say I cut a lot for a hobby shop, 4 hours a night average and the book has been great on carbon and aluminum.
DIY 5x10 v rail, rack and pinion
Gecko g540
Pm65 - aka game changer
Longevity ForceCut 42i is sitting on the shelf
Proma THC
ACAD, SheetCam, Mach3
Millermatic 211
NEW HORSE IN THE STABLE:
4'x8' LDR downdraft w/a scribe
Milltronics Partner 2 CNC mill
Gecko g540
Pm65 - aka game changer
Longevity ForceCut 42i is sitting on the shelf
Proma THC
ACAD, SheetCam, Mach3
Millermatic 211
NEW HORSE IN THE STABLE:
4'x8' LDR downdraft w/a scribe
Milltronics Partner 2 CNC mill
- tnbndr
- 4.5 Star Elite Contributing Member
- Posts: 1690
- Joined: Mon Jan 09, 2012 4:30 pm
- Location: New Berlin, WI
- Contact:
Re: Torchmate X 5x10 - Hypotherm PM85 - .750 plate ... what should i expect?
I always start with the PM manual suggested settings. A lot of researcha and testing went into arriving at those settings.
If things aren't exactly right play around from there.
If things aren't exactly right play around from there.
Dennis
LDR 4x8, Scribe, DTHCIV
Hypertherm PM45, Macair Dryer
DeVilbiss Air America 6.5HP, 80Gal., 175psi, Two Stage
16.9scfm@100psi, 16.0scfm@175psi
Miller 215 MultiMatic
RW 390E Slip Roll (Powered)
AutoCAD, SheetCAM, Mach 3
http://ikescreations.com
LDR 4x8, Scribe, DTHCIV
Hypertherm PM45, Macair Dryer
DeVilbiss Air America 6.5HP, 80Gal., 175psi, Two Stage
16.9scfm@100psi, 16.0scfm@175psi
Miller 215 MultiMatic
RW 390E Slip Roll (Powered)
AutoCAD, SheetCAM, Mach 3
http://ikescreations.com
-
- 5 Star Elite Contributing Member
- Posts: 3087
- Joined: Mon Jul 20, 2009 11:18 pm
- Location: North Carolina
Re: Torchmate X 5x10 - Hypotherm PM85 - .750 plate ... what should i expect?
I recommend getting an air compressor with a 60 to 80 gallon receiver tank, and a flow rating @90 psi at roughly double the requirement for the Powermax85. The plasma requires 6.7 cfm @90 psi, so somewhere around 13 to 14 cfm@90 is a good choice. Other things to look for in a compressor:
- Industrial quality compressors use electric motors that run at about 1725 RPM, lower quality compressors run at about 3450 RPM. The lower RPM compressor will be quieter, will last longer, and will cost more. Worth every penny.
-The Powermax85 needs inlet pressure when air is flowing at the torch to stay between 90 and 135 psi. Lower will affect cut quality, higher will damage internal components. Industrial compressors generally have on/off cycles set at 90 to 120 psi. If yours goes above 135 it will need a pressure regulator to not allow pressure above 135 psi.
- Install a pressure gauge right on the inlet fitting of the Powermax85 so you can monitor input pressure.....the one back at the compressor will not show the true inlet pressure due to pressure drop through your plumbing.
-It is always a good idea to drain the compressor tank daily. Even a better idea to install an auto drain.
-If you are in a humid environment, you may need some moisture removal equipment that can range from an absorbing filter to a coalescing trap to a dessicant dryer to a refrigerated dryer. They ones toward the right of my last sentence work best and cost more. If you are in a dry climate or only cut occasionally you may not need any moisture removal devices.
The 3/4" lifting lug in my previous post was cut exactly with all specs right out of the Hypertherm operators manual at 85 amps. You will be hard pressed to improve on the specs in the manual. The critical specs are: Pierce height, pierce delay, cut height, cut speed. Use the arc voltage setting from the manual with your AVHC to adjust the height until the physical cut height is correct. Often with the Torchmate AVHC the listed voltage will need to be adjust higher or lower than the suggested setting in order to achieve the correct physical cut height.
Jim Colt Hypertherm
- Industrial quality compressors use electric motors that run at about 1725 RPM, lower quality compressors run at about 3450 RPM. The lower RPM compressor will be quieter, will last longer, and will cost more. Worth every penny.
-The Powermax85 needs inlet pressure when air is flowing at the torch to stay between 90 and 135 psi. Lower will affect cut quality, higher will damage internal components. Industrial compressors generally have on/off cycles set at 90 to 120 psi. If yours goes above 135 it will need a pressure regulator to not allow pressure above 135 psi.
- Install a pressure gauge right on the inlet fitting of the Powermax85 so you can monitor input pressure.....the one back at the compressor will not show the true inlet pressure due to pressure drop through your plumbing.
-It is always a good idea to drain the compressor tank daily. Even a better idea to install an auto drain.
-If you are in a humid environment, you may need some moisture removal equipment that can range from an absorbing filter to a coalescing trap to a dessicant dryer to a refrigerated dryer. They ones toward the right of my last sentence work best and cost more. If you are in a dry climate or only cut occasionally you may not need any moisture removal devices.
The 3/4" lifting lug in my previous post was cut exactly with all specs right out of the Hypertherm operators manual at 85 amps. You will be hard pressed to improve on the specs in the manual. The critical specs are: Pierce height, pierce delay, cut height, cut speed. Use the arc voltage setting from the manual with your AVHC to adjust the height until the physical cut height is correct. Often with the Torchmate AVHC the listed voltage will need to be adjust higher or lower than the suggested setting in order to achieve the correct physical cut height.
Jim Colt Hypertherm
Jeebus wrote:at the price im getting this machine, its going to put me ahead of the game for sure.
Could you also help me out with another thing... I want to get an air compressor to dedicate to the table to run the plasma. What would you reccomend.
I think the water jet cost about 250k new, and its fantastic, but its often not needed.... which is what led me to find this plasma deal, and i just dont think i can go wrong with it. I really would like to be able to cut .750 plate, can you reccomend some settings to start with? or just go with the PM guide settings?
-
- 1 Star Member
- Posts: 13
- Joined: Wed Jun 17, 2015 9:53 am
Re: Torchmate X 5x10 - Hypotherm PM85 - .750 plate ... what should i expect?
Thanks for all the help everyone, greatly appreciated!
-
- 1 Star Member
- Posts: 13
- Joined: Wed Jun 17, 2015 9:53 am
Re: Torchmate X 5x10 - Hypotherm PM85 - .750 plate ... what should i expect?
Just a quick update to this, and some more questions....
I have gotten my .250 plate and .500 plate specs dialed in on the machine, and im so impressed with the cut quality using pretty much the exact specs that the hypotherm manual suggests. Honestly, i cant even explain how happy i am with these results.
Now, ive been spending the full day with .750 plate, and im far far far less impressed, almost disappointed to be honest. When i use the recommended settings on the manual for this to set my baseline, i was having issues even having the material cut all the way through. I did some adjusting and slowed my speeds down a bit, and im now cutting all the way through but the slag/dros on the bottom is nearly 1" long, thick and very tough, the kerf is also terrible also.
When i run a voltage test, it shows to cut at roughly 120 volts, when the manual calls for 134volts. im also cutting this with coolant on the table also, if that matters.
Any suggestions what i should be trying next? I would love to dial this in as well, but every little change ive made so far has been worse and wrose.

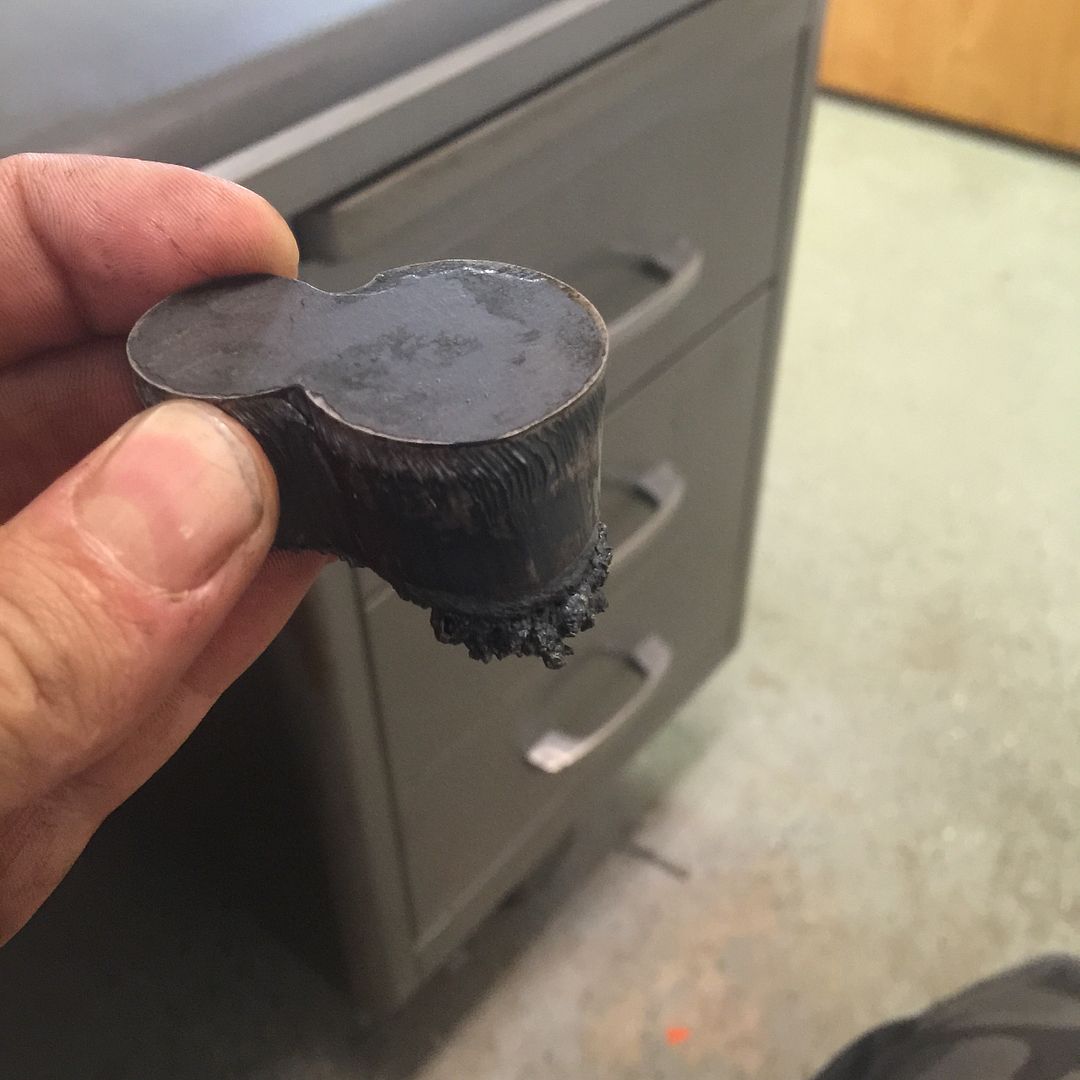
I have gotten my .250 plate and .500 plate specs dialed in on the machine, and im so impressed with the cut quality using pretty much the exact specs that the hypotherm manual suggests. Honestly, i cant even explain how happy i am with these results.
Now, ive been spending the full day with .750 plate, and im far far far less impressed, almost disappointed to be honest. When i use the recommended settings on the manual for this to set my baseline, i was having issues even having the material cut all the way through. I did some adjusting and slowed my speeds down a bit, and im now cutting all the way through but the slag/dros on the bottom is nearly 1" long, thick and very tough, the kerf is also terrible also.
When i run a voltage test, it shows to cut at roughly 120 volts, when the manual calls for 134volts. im also cutting this with coolant on the table also, if that matters.
Any suggestions what i should be trying next? I would love to dial this in as well, but every little change ive made so far has been worse and wrose.

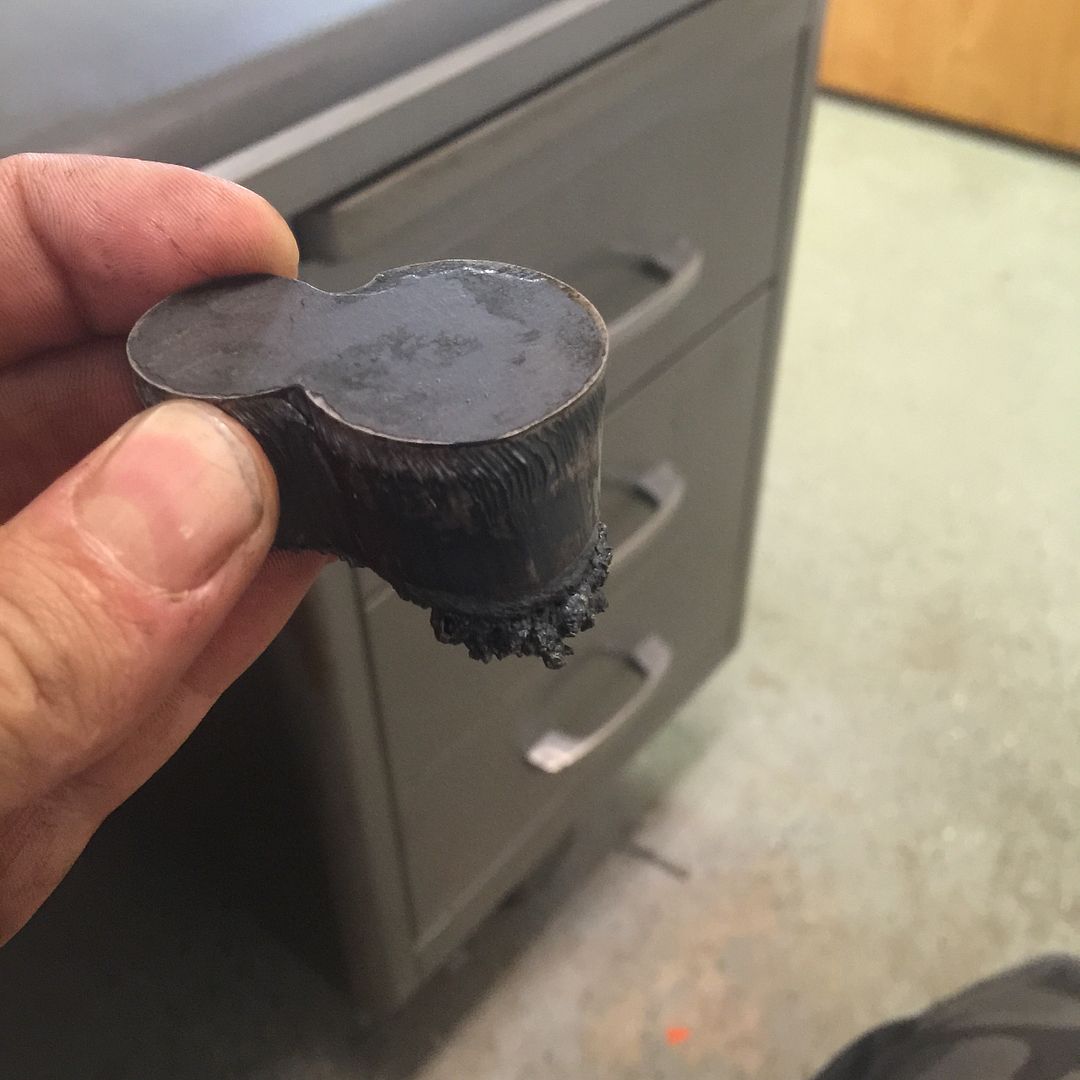
Last edited by Jeebus on Sat Sep 12, 2015 8:49 am, edited 1 time in total.
-
- 3 Star Member
- Posts: 345
- Joined: Mon Feb 23, 2015 5:23 pm
- Location: Austin, TX
Re: Torchmate X 5x10 - Hypotherm PM85 - .750 plate ... what should i expect?
Can you post some pictures? I don't have any experience with .750, but I think the pictures would be helpful in seeing what's going on.
-
- 1 Star Member
- Posts: 13
- Joined: Wed Jun 17, 2015 9:53 am
Re: Torchmate X 5x10 - Hypotherm PM85 - .750 plate ... what should i expect?
Here are some samples, and i know these are small, its just all i had left to take a picture of. Even when its a larger 6x6 square, the slag is still the same, and the cut quality is still the same.
Thanks!
EDIT.
Nevermind, i guess i cannot attach or upload photos here. I will see if i can find a way.
Thanks!
EDIT.
Nevermind, i guess i cannot attach or upload photos here. I will see if i can find a way.
- acourtjester
- 6 Star Elite Contributing Member
- Posts: 8165
- Joined: Sat Jun 02, 2012 6:04 pm
- Location: Pensacola, Fla
Re: Torchmate X 5x10 - Hypotherm PM85 - .750 plate ... what should i expect?
down below the message section is a tab marked attachments click on it and then you just move to the location on you computer (folder) and click on the image you want to attach. It is limited to size but it will tell you if it is to large you can only attach jpeg and bmp images and DFX/SVG files or you can ZIP them.
DIY 4X4 Plasma/Router Table
Hypertherm PM65 Machine Torch
Drag Knife and Scribe
Miller Mig welder
13" metal lathe
Small Mill
Everlast PowerTig 255 EXT
Hypertherm PM65 Machine Torch
Drag Knife and Scribe
Miller Mig welder
13" metal lathe
Small Mill
Everlast PowerTig 255 EXT
-
- 1 Star Member
- Posts: 13
- Joined: Wed Jun 17, 2015 9:53 am
Re: Torchmate X 5x10 - Hypotherm PM85 - .750 plate ... what should i expect?
Yea, i do that, and press submit, but the photos dont show up in the post.... did it again in this one, and i dont see them...?
-
- 4 Star Member
- Posts: 764
- Joined: Wed Aug 13, 2014 8:30 am
- Location: Hertfordshire, England
- Contact:
Re: Torchmate X 5x10 - Hypotherm PM85 - .750 plate ... what should i expect?
Jeebus wrote: When i run a voltage test, it shows to cut at roughly 120 volts, when the manual calls for 134volts. im also cutting this with coolant on the table also, if that matters.
AS far as I have learnt so far, low power(<200A) plasma does not like wet cutting, above or below the plate. Try with a dry plate and clearance below from the water surface.
-
- 5 Star Elite Contributing Member
- Posts: 3087
- Joined: Mon Jul 20, 2009 11:18 pm
- Location: North Carolina
Re: Torchmate X 5x10 - Hypotherm PM85 - .750 plate ... what should i expect?
What you are showing in the pics is low speed dross......this is caused by cutting too slow. Since it sounds like you are paying attention to voltage, not cut height.....that likely is the problem.
T cut 3/4" steel with the Hypertherm 85 amp process:
1. Set cut speed to 24 ipm.
2. Set pierce height to .24". (verify that the pierce height is correct. Slightly higher is ok, lower is not ok!)
3. pierce delay time to 1.5 seconds. (this should be long enough so the arc is blowing sparks out the bottom of the material before any x, y or z movement occurs, torch still at pierce height. (a little to long is ok, to short is not)
4. Set cut height to .06" (1/16")
5. Assuming all of the above is correct....put the height control in manual, pierce the plate, cut a short distance and monitor the arc voltage, verifying that the torch is .060" off the material. Use the voltage that you monitored (what the readout said with the torch cutting at the above specs (24 ipm, torch .06" off the plate) for your preset voltage then proceed to cut with height control in automatic.
I suspect one or more of the following caused the torch to not cut through all the way.....then you decided that slower speed was necessary...the slow speed will make dross that looks just like the dross in your picture.
- If you were setting the height control to the voltage setting in the cut chart...and did not verify that that kept the torch at .06", then you likely would not fully penetrate the material....and would have had to slow down. Many systems have height controls that are not accurately calibrated....so in that case you need to do a cut test at book settings as I listed above,,,,,to determine the arc voltage that will maintain the cut height. Height is important, the voltage is just the feedback mechanism that controls the height.
- It is possible that you had a damaged nozzle orifice....which can occur on the first pierce on 3/4" material if not done correctly. A damaged nozzle will cause heavy dross, and will cause you to slow down to try and penetrate the plate. Inspect the nozzle and shield (make sure you are using the mechanized shield) per the consumables inspection section in the operators manual.
The above specs are from the operators manual for the Powermax, I stand behind the fact that they will produce a nice cut on 3/4" steel. The voltages listed in the manual are correct when operating at book specs with consumables in un-damaged condition......and the height control is providing an accurate voltage......we use all laboratory grade test equipment to develop the voltage specs.
Best regards, Jim Colt Hypertherm
T cut 3/4" steel with the Hypertherm 85 amp process:
1. Set cut speed to 24 ipm.
2. Set pierce height to .24". (verify that the pierce height is correct. Slightly higher is ok, lower is not ok!)
3. pierce delay time to 1.5 seconds. (this should be long enough so the arc is blowing sparks out the bottom of the material before any x, y or z movement occurs, torch still at pierce height. (a little to long is ok, to short is not)
4. Set cut height to .06" (1/16")
5. Assuming all of the above is correct....put the height control in manual, pierce the plate, cut a short distance and monitor the arc voltage, verifying that the torch is .060" off the material. Use the voltage that you monitored (what the readout said with the torch cutting at the above specs (24 ipm, torch .06" off the plate) for your preset voltage then proceed to cut with height control in automatic.
I suspect one or more of the following caused the torch to not cut through all the way.....then you decided that slower speed was necessary...the slow speed will make dross that looks just like the dross in your picture.
- If you were setting the height control to the voltage setting in the cut chart...and did not verify that that kept the torch at .06", then you likely would not fully penetrate the material....and would have had to slow down. Many systems have height controls that are not accurately calibrated....so in that case you need to do a cut test at book settings as I listed above,,,,,to determine the arc voltage that will maintain the cut height. Height is important, the voltage is just the feedback mechanism that controls the height.
- It is possible that you had a damaged nozzle orifice....which can occur on the first pierce on 3/4" material if not done correctly. A damaged nozzle will cause heavy dross, and will cause you to slow down to try and penetrate the plate. Inspect the nozzle and shield (make sure you are using the mechanized shield) per the consumables inspection section in the operators manual.
The above specs are from the operators manual for the Powermax, I stand behind the fact that they will produce a nice cut on 3/4" steel. The voltages listed in the manual are correct when operating at book specs with consumables in un-damaged condition......and the height control is providing an accurate voltage......we use all laboratory grade test equipment to develop the voltage specs.
Best regards, Jim Colt Hypertherm
Jeebus wrote:Just a quick update to this, and some more questions....
I have gotten my .250 plate and .500 plate specs dialed in on the machine, and im so impressed with the cut quality using pretty much the exact specs that the hypotherm manual suggests. Honestly, i cant even explain how happy i am with these results.
Now, ive been spending the full day with .750 plate, and im far far far less impressed, almost disappointed to be honest. When i use the recommended settings on the manual for this to set my baseline, i was having issues even having the material cut all the way through. I did some adjusting and slowed my speeds down a bit, and im now cutting all the way through but the slag/dros on the bottom is nearly 1" long, thick and very tough, the kerf is also terrible also.
When i run a voltage test, it shows to cut at roughly 120 volts, when the manual calls for 134volts. im also cutting this with coolant on the table also, if that matters.
Any suggestions what i should be trying next? I would love to dial this in as well, but every little change ive made so far has been worse and wrose.
-
- 1 Star Member
- Posts: 13
- Joined: Wed Jun 17, 2015 9:53 am
Re: Torchmate X 5x10 - Hypotherm PM85 - .750 plate ... what should i expect?
Thanks for the help!
I went into this again this morning, with a clear mind after being frustrated last week with it, and i was able to get partial success....
I went back and set everything to the settings you suggested and in the manual, and checked the height of my cut. It appears correct at .06 with the shim selection i have for the mill.
So, i tried the cut at the suggested speed, and at the suggested voltage, in manual mode on the height control. It pierced good, and cut an inch or so, and it was clearly reading at about 122 volts or so.... So, i paused the cut, changed the voltage, and then put it in Auto mode. Started up the cut again, and this is what i had happen. the head came down, touched the material, came up to pierce height, fired up the machine, pierced the material fine all the way through, then went down to the cut height, and moved about 1/4" into the cut line and the head just dove down into the material, and my cutting head came off the magnets. Well, this exact process happened a few times, before i decided to try something different...
I decided to keep all the settings the same as the manual suggests, put the voltage back to the settings in the manual. then i put my height controller at manual cut instead of auto, and cut the part out. Now, with this process, everything went well...ish. As you can see from the photo, it cuts in some places great, but in others i get this blowback up through the cut line, and it bubbles up and hardens onthe top as you can see in some places here.
thanks again for all the help, hands down you have some of the best support i have ever experienced.
Taylor
I went into this again this morning, with a clear mind after being frustrated last week with it, and i was able to get partial success....
I went back and set everything to the settings you suggested and in the manual, and checked the height of my cut. It appears correct at .06 with the shim selection i have for the mill.
So, i tried the cut at the suggested speed, and at the suggested voltage, in manual mode on the height control. It pierced good, and cut an inch or so, and it was clearly reading at about 122 volts or so.... So, i paused the cut, changed the voltage, and then put it in Auto mode. Started up the cut again, and this is what i had happen. the head came down, touched the material, came up to pierce height, fired up the machine, pierced the material fine all the way through, then went down to the cut height, and moved about 1/4" into the cut line and the head just dove down into the material, and my cutting head came off the magnets. Well, this exact process happened a few times, before i decided to try something different...
I decided to keep all the settings the same as the manual suggests, put the voltage back to the settings in the manual. then i put my height controller at manual cut instead of auto, and cut the part out. Now, with this process, everything went well...ish. As you can see from the photo, it cuts in some places great, but in others i get this blowback up through the cut line, and it bubbles up and hardens onthe top as you can see in some places here.
thanks again for all the help, hands down you have some of the best support i have ever experienced.
Taylor
- Attachments
-
- IMG_3873 (1).JPG (134.46 KiB) Viewed 2444 times
- IMG_3873 (1).JPG (134.46 KiB) Viewed 2444 times
-
- 1 Star Member
- Posts: 13
- Joined: Wed Jun 17, 2015 9:53 am
Re: Torchmate X 5x10 - Hypotherm PM85 - .750 plate ... what should i expect?
also, upon further inspection of this, the part is not cut all the way through in some spots, once i flipped the part over to the bottom side i could see about 3 areas, about 2" long in line segment, that were not cut all the way through.
-
- 4 Star Member
- Posts: 764
- Joined: Wed Aug 13, 2014 8:30 am
- Location: Hertfordshire, England
- Contact:
Re: Torchmate X 5x10 - Hypotherm PM85 - .750 plate ... what should i expect?
Is it possible to try a re-run with the water level about 2" lower??
- Gamelord
- 4.5 Star Member
- Posts: 1636
- Joined: Wed Aug 29, 2012 5:17 pm
- Contact:
Re: Torchmate X 5x10 - Hypotherm PM85 - .750 plate ... what should i expect?
I may take a look at your air supplyy, double and triple checking that you are not having pressure drops or water/oil.
Once you take flight, your eyes will forever be turned to the sky." "Lack of appreciation is the worlds biggest crime."
Torchmate 6x14 w/THC Downdraft
Thermal Dynamics Cutmaster 101
Corel Draw / Adobe Illustrator
Torchmate CAD
Torchmate 6x14 w/THC Downdraft
Thermal Dynamics Cutmaster 101
Corel Draw / Adobe Illustrator
Torchmate CAD
-
- 1 Star Member
- Posts: 13
- Joined: Wed Jun 17, 2015 9:53 am
Re: Torchmate X 5x10 - Hypotherm PM85 - .750 plate ... what should i expect?
Air supply is good, and dry. My compressor did not even kick on during this cut, volume stayed above 120 the whole time.
The air seems dry, but I guess I'm not 100% sure how to test this. I have an cooler, and it works properly, it looks clean and dry.
I can try another cut tomorrow with the water levels lower also
The air seems dry, but I guess I'm not 100% sure how to test this. I have an cooler, and it works properly, it looks clean and dry.
I can try another cut tomorrow with the water levels lower also
-
- 4 Star Member
- Posts: 764
- Joined: Wed Aug 13, 2014 8:30 am
- Location: Hertfordshire, England
- Contact:
Re: Torchmate X 5x10 - Hypotherm PM85 - .750 plate ... what should i expect?
Place a clean mirror under the nozzle and put the torch into test mode so only air flows, any oil or water will be seen on the glass, run test for a few minutes.