So many cutting issues. Going to pull my hair out
-
- 4 Star Member
- Posts: 950
- Joined: Thu Jan 02, 2014 6:33 pm
Re: So many cutting issues. Going to pull my hair out
lol sorry I meant 0.03-0.05
Torchmate 2x2 - Flashcut
Powermax 45 - Machine torch
Taig CNC Mill - Flashcut
Razorweld Distributor
Powermax 45 - Machine torch
Taig CNC Mill - Flashcut
Razorweld Distributor
-
- 1 Star Member
- Posts: 16
- Joined: Sun Nov 02, 2014 4:08 pm
Re: So many cutting issues. Going to pull my hair out
Any updates on getting things sorted out gamble?
ill be trying my luck with my 42i forcecut next year curious if you found the solution to your air woes?
ill be trying my luck with my 42i forcecut next year curious if you found the solution to your air woes?
-
- 4 Star Member
- Posts: 950
- Joined: Thu Jan 02, 2014 6:33 pm
Re: So many cutting issues. Going to pull my hair out
Haven't touched my machine in over a week to be honest. Once I save some cash I'm going to buy the hypertherm air filtration system. A little pricey at $195 (ish) but I was really impressed the quality and I think that will help solve some issues.motofool33 wrote:Any updates on getting things sorted out gamble?
ill be trying my luck with my 42i forcecut next year curious if you found the solution to your air woes?
Torchmate 2x2 - Flashcut
Powermax 45 - Machine torch
Taig CNC Mill - Flashcut
Razorweld Distributor
Powermax 45 - Machine torch
Taig CNC Mill - Flashcut
Razorweld Distributor
-
- 2.5 Star Member
- Posts: 150
- Joined: Sat Feb 23, 2013 12:24 am
Re: So many cutting issues. Going to pull my hair out
I use to use a longevity 50i..and got really great results..i think i got better cut quality and pierced faster than my hypertherm powermax45..with the 50i i would run the air pressure around 100psi and run the voltage at 50.. for 1/4 inch i would run at 50 ipm pierce time i ran .4....The hypertherm pm45 cuts at faster speeds and is more reliable then the longevity was-better torch design.. The trafimet was good but would stick sometimes causing the torch not to fire reliably...With the hypertherm pm45 i run my pressure maxed out with it on 45 amps pierce time at .5.cutting at 65ipm i get good results on 1/4 inch..So basically turn your power up it takes at least 50 amps to cut 1/4 inch steel.and the pressure will need to be around 100 psi to be able to pierce
-
- 4 Star Member
- Posts: 950
- Joined: Thu Jan 02, 2014 6:33 pm
Re: So many cutting issues. Going to pull my hair out
Well now i think i broke a bearing on the table. so it's on the back burner.
And as of 10 minutes ago my car just broke. FML
And as of 10 minutes ago my car just broke. FML
Torchmate 2x2 - Flashcut
Powermax 45 - Machine torch
Taig CNC Mill - Flashcut
Razorweld Distributor
Powermax 45 - Machine torch
Taig CNC Mill - Flashcut
Razorweld Distributor
-
- 2.5 Star Member
- Posts: 150
- Joined: Sat Feb 23, 2013 12:24 am
Re: So many cutting issues. Going to pull my hair out
I did something like this for my system and it worked wonders..I have a automatic drain on my compressor.(60 gallon 7.5 hp) then i have a water separator on the compressor.From there the 3/4 inch air line runs up and along the ceiling to the other side of my shop about 50ft of run.then it drops down about 4 ft from the floor where i run over 4 ft then i have a t the air line goes back up to the ceiling and the other part of the t goes to the floor with a drain valve.the air line then goes back across the shop to another 2 water separators near the plasma cutter..after doing this with the air lines i have never seen any moisture in the secondary and final water separators.. i just open the drain valve daily on my wall drop and i am good to go..Giving the air a chance to cool down and then making it go up and down lets gravity do most of the work of drying out the air.
quote="_Ogre"]it sounds like moisture is your first concern, fix that and other problems may be minor
before running out and buying a refrigerated air dryer, even those need cooled dry air in them or they get overloaded
i suspect your running a 3/8'' rubber hose from the compressor to the plasma table, not a good idea
buy 40 feet of 3/4'' copper tube and a fist full of 90*s to make up a one of these air cooler/dryer loops
1/2'' copper would probably work just as well with your compressor for less money, also less surface area
air in the top, slope all tubing to the bottom to a T, drip leg down to a valve and up with dry(er) air
if you block walls in your shop fasten your new air cooler/dryer to the block wall for a heat sink
it doesn't have to be just like the pic, it's just a pic i downloaded. maybe 20 ft of copper in this
shorten the drops, 90* down, street el 90* back (or short nipple and 90* back) and just as wide as you can get it
make it look like this
air in on top
l___________________________
___________________________l use shortest drops as possible
l___________________________
___________________________l
l___________________________
___________________________l make it a 3 feet wide or wider
l___________________________
___________________________l
l air out up
l
l
l drain valve at bottom of drip leg
if that^^^ makes any sense
even if you buy a refrigerated air dry this will cool and dry the air feeding into the dryer
you should be able to get rid of the desiccant in your system, save the desiccant for spraying paint
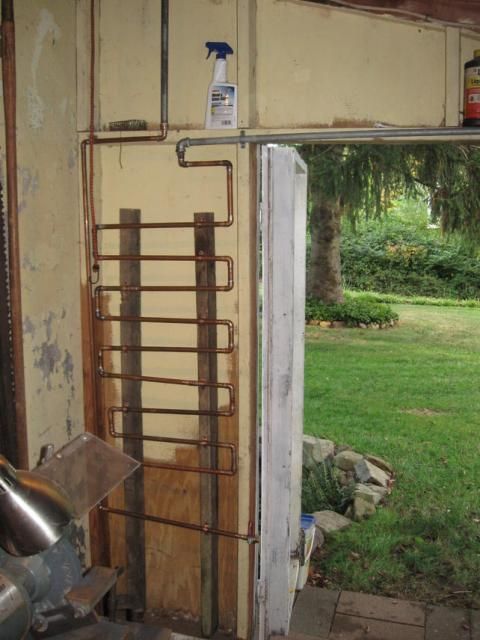
this is our setup in a commercial shop with plasma table, 3 techs, 3 lifts, painter and paint booth
we have 60 feet of 1'' steel line before any air distribution
yes we use desiccant at the paint booth it lasts 3 months before we change the desiccant
[/quote]
quote="_Ogre"]it sounds like moisture is your first concern, fix that and other problems may be minor
before running out and buying a refrigerated air dryer, even those need cooled dry air in them or they get overloaded
i suspect your running a 3/8'' rubber hose from the compressor to the plasma table, not a good idea
buy 40 feet of 3/4'' copper tube and a fist full of 90*s to make up a one of these air cooler/dryer loops
1/2'' copper would probably work just as well with your compressor for less money, also less surface area
air in the top, slope all tubing to the bottom to a T, drip leg down to a valve and up with dry(er) air
if you block walls in your shop fasten your new air cooler/dryer to the block wall for a heat sink
it doesn't have to be just like the pic, it's just a pic i downloaded. maybe 20 ft of copper in this
shorten the drops, 90* down, street el 90* back (or short nipple and 90* back) and just as wide as you can get it
make it look like this
air in on top
l___________________________
___________________________l use shortest drops as possible
l___________________________
___________________________l
l___________________________
___________________________l make it a 3 feet wide or wider
l___________________________
___________________________l
l air out up
l
l
l drain valve at bottom of drip leg
if that^^^ makes any sense

even if you buy a refrigerated air dry this will cool and dry the air feeding into the dryer
you should be able to get rid of the desiccant in your system, save the desiccant for spraying paint
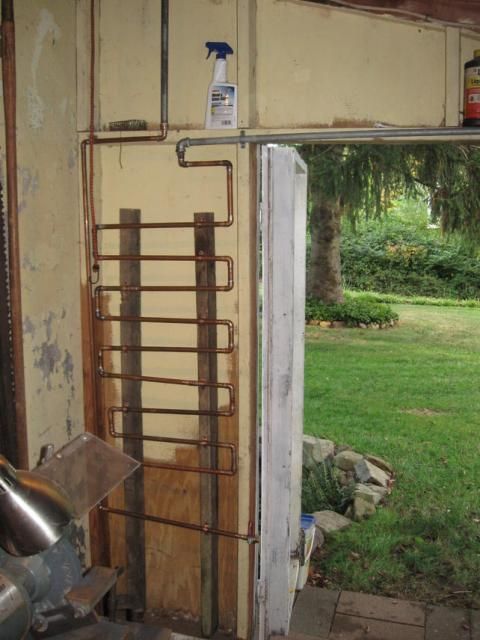
this is our setup in a commercial shop with plasma table, 3 techs, 3 lifts, painter and paint booth
we have 60 feet of 1'' steel line before any air distribution
yes we use desiccant at the paint booth it lasts 3 months before we change the desiccant
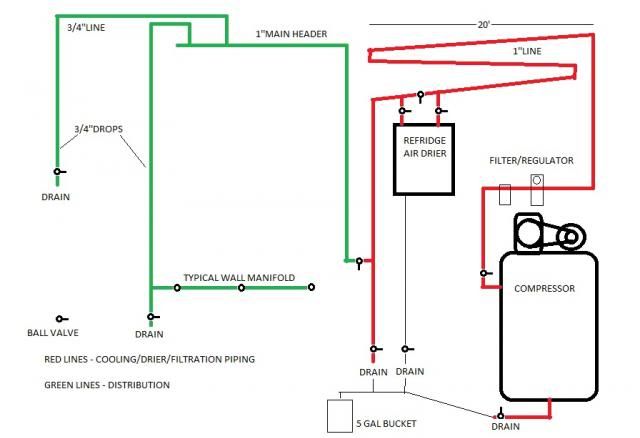