top: cut all the way around, .1'' lead in/out, 38ipm, 131v, 65 amps, .15 pierce ht. no dross, the .44 hole dropped out but that's not always the case
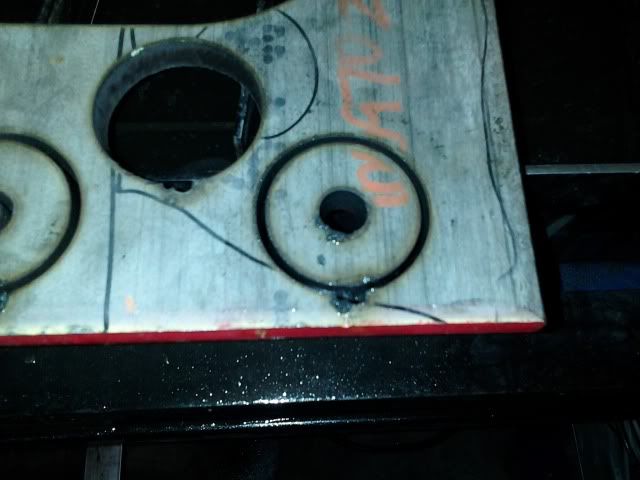
bottom: not cut all the way, minimal dross
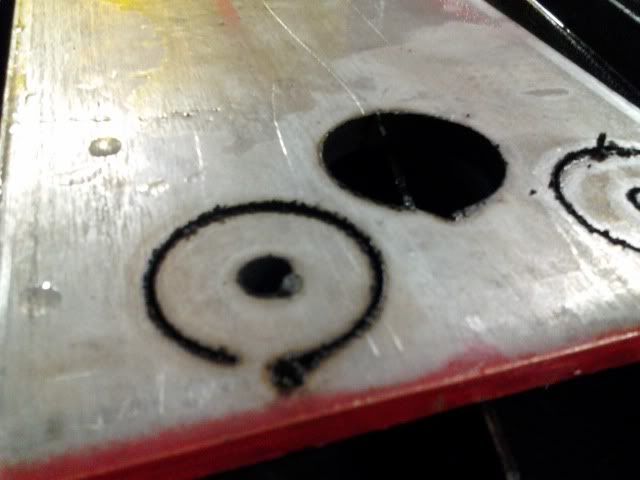
i've tried speeds from 38 to 45 ipm. have not varied the volts or amps.
i believe i'm having a similar problem to what jhart is having in this thread http://plasmaspider.com/viewtopic.php?f=4&t=12343
we needed 2 flanges to do a build in the morning so i cut them both. this is the bottom. 38ipm, 65a, 131v, .1 lead in, no lead out and a .1 delay at the end of cut. not sure mach3 can slow at the end of the cut as suggested by jim colt in the thread posted. small holes still connected.
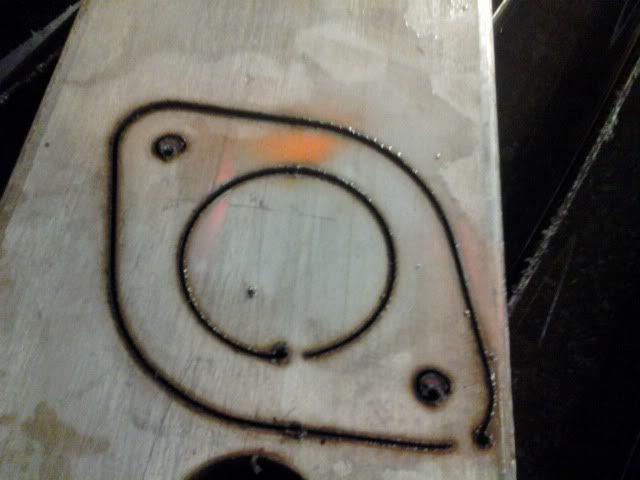
any other suggestions to try?