On some of the lead ins you can see where it looked like the torch dwelled to long, I have 0 for lead in delay but you can see the spot on the letters where the lead in was. Using arch .125 lead in.
Also have a few other problems as you can see, cutting on a precision plasma 4 X 8 table with CNC 620 motors with Ron's gear reduction units.
Jim, and gang any input is appreciated

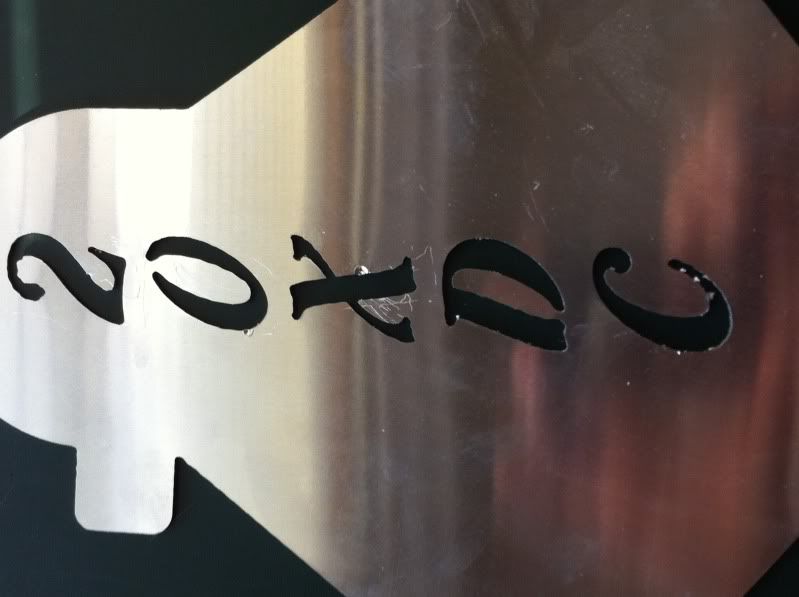
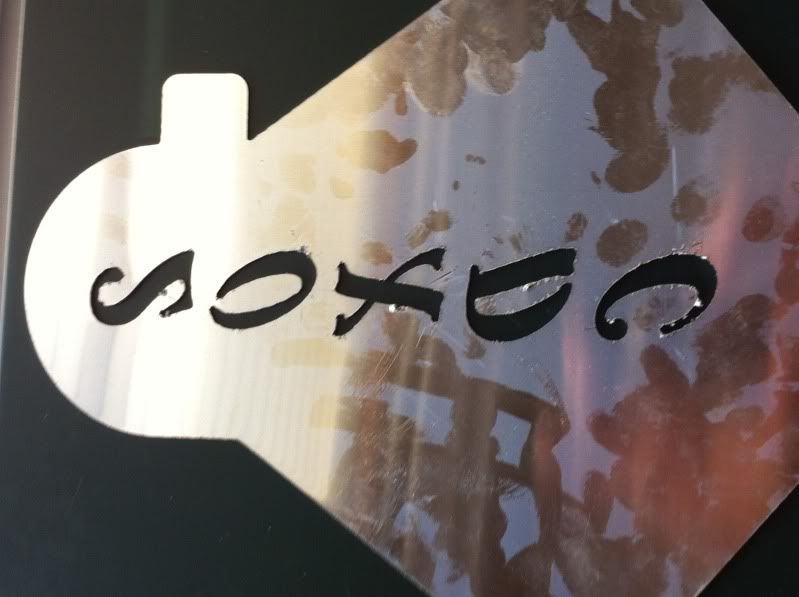
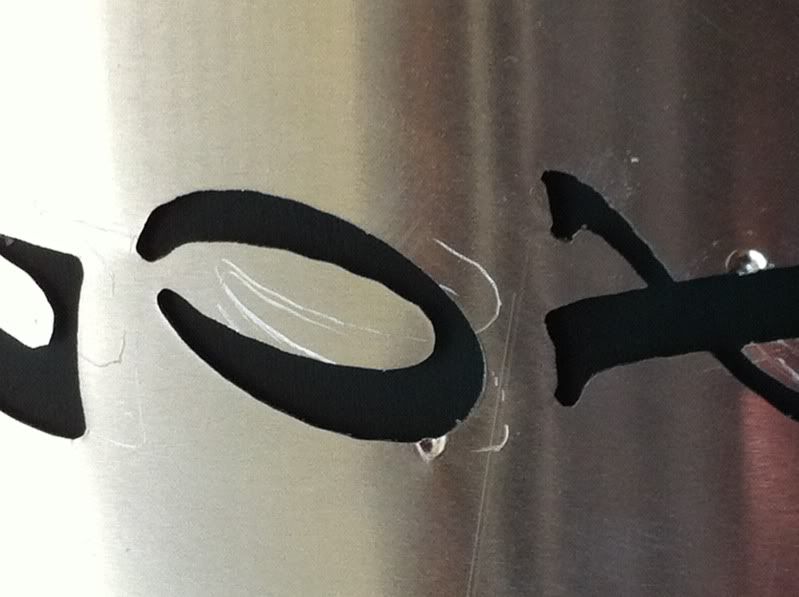