I'm have limited experience cutting 1/2" material. I had my 2nd 1/2" job yesterday...same customer as my first 1/2" job. I fought this damned job FAR longer than I should have. The primary issue is keeping the torch from getting knocked off the mag-mount by the slag pile, post-pierce. I was cutting some 1" diameter circles, piercing in the center. I ended up babysitting every cut, making sure the torch didn't grab a slag pile, and get pulled over. I learned this after losing 3 tips to this issue. :/ Sometimes I would try to scrape the slag pile out of the way, sometimes I'd just hold the torch so it didn't get knocked over as it lightly kissed the top of the pile. NOT what I'm used to when cutting my 18ga-3/16 materials! I can essentially walk away from the table on those.
I ended up using Les' "pierce only" post in Sheet cam. Meaning, I put an old nozzle/electrode in, and pierced the holes for the lead in. Then I put in a good nozzle/electrode, went back and generated a cut file, and cut the part. This helped with the "torch tip snags on the pile" problem, but it then posed a new issue. With the pre-pierced material gone (crater there), the arc would often not find the material, so during the actual cut process the torch would just sit there and blow a pilot arc until it shut down. I fixed this problem by shutting off the THC, so the torch would start moving without the THC waiting to "find and arc". That's fine on the small circles, where I don't want THC anyway, but not something to be used on the larger/longer perimeter cuts. I was manually kicking the THC back on after the arc connected (when it moves past the pierce area).
I then tried a "pierce only" of about 1/2" the regular pierce time. This created a nice divot, but did not blow through the material. On the "cut" file, I also did a pierce, also for a shorter duration than normal. This would generally let the arc form (so I could use THC), and it generally created a smaller slag pile on the material (since 1/2 or more of the material had already been blown out). However, this pile was often STILL large enough to catch the torch tip.
Lastly, the non-stop fight of angularity. First several cuts were fine, then I had a tip crash (see above). After that, I had angularity. I replaced the nozzle, shield, swirl ring, and o-ring. No change. Made sure torch was still square. Finally, replaced the CopperPlus electrode I was using, which looked fine. Angularity problem went away. I swear...I am so damn tired of fighting angularity on 1/2" material! Then again, it probably wouldn't have become an issue, had all the tip-hangs not happened (blowing crap into the shield holes, blowing out nozzles, and letting debris blow up into the electrode).
Anyway...I'm getting ready to clean up some of these cuts, and let the customer know they're ready for pickup. In the meantime, I'd be very appreciative of any tips or tricks shared by those of you who regularly make 1/2" cuts with good results.
Oh, BTW, I was cutting using the 45A process (to reduce angularity..har har). 45A, 18ipm, 141v.
Those of you who regularly cut 1/2 and thicker stuff...Q.
-
- 4 Star Elite Contributing Member
- Posts: 1184
- Joined: Tue Aug 25, 2015 12:05 pm
- Location: Central MO, USA
Those of you who regularly cut 1/2 and thicker stuff...Q.
Last edited by motoguy on Wed Apr 12, 2017 4:46 pm, edited 1 time in total.
Bulltear 6x12 w/ Proton Z axis & watertable
CommandCNC/Linux w/ Ohmic & HyT options
Hypertherm Powermax 85 w/ machine torch
Solidworks, Coreldraw X7, Inkscape, Sheetcam
CommandCNC/Linux w/ Ohmic & HyT options
Hypertherm Powermax 85 w/ machine torch
Solidworks, Coreldraw X7, Inkscape, Sheetcam
-
- 2 Star Member
- Posts: 54
- Joined: Sat Aug 13, 2016 9:50 am
Re: Those of you who regularly cut 1/2 and thicker stuff...Q.
Spray the plate with anti-spatter.
- SeanP
- 4 Star Member
- Posts: 951
- Joined: Thu Aug 01, 2013 11:50 am
- Location: Co Kerry, Ireland
Re: Those of you who regularly cut 1/2 and thicker stuff...Q.
Trouble is waterbased anti spatter does't work well with a water table, what I do is spray the sheet with a mist of a product called duck oil made by swarfega, it's not really for that but it definitely works, it could be the lanolin in it?
Another one for a few holes is to dab mig tip dip on the pierce area with a brush, bit slow for a big job, where as spraying the whole sheet I don't have any worries of slag piles, angularity is still the same problem, drives you mad!
I thought the 85 was the bees knees and better than my 45! are you sure your pierce height is reading accurate? with the 45 I use a 4mm pierce height rather than 3.8mm (book height) be sure you have a long enough pierce delay time as well.
That tip dip is a godsend on the shield and retaining cap as well, paint it on with a brush right up to the torch, it's completely stopped me wrecking retaining caps, seems to waterproof the area that was breaking down with me on previous ones.
It really keeps the shield clean as well, brush it on cold or warm even when cutting.
One other thing I have learned (only recently even though I read about it ages ago) is not to tighten the retaining cap to tight, just light/finger tight or it seems to stop the electrode sliding in the swirl ring and causing misfire/fault.
Another one for a few holes is to dab mig tip dip on the pierce area with a brush, bit slow for a big job, where as spraying the whole sheet I don't have any worries of slag piles, angularity is still the same problem, drives you mad!
I thought the 85 was the bees knees and better than my 45! are you sure your pierce height is reading accurate? with the 45 I use a 4mm pierce height rather than 3.8mm (book height) be sure you have a long enough pierce delay time as well.
That tip dip is a godsend on the shield and retaining cap as well, paint it on with a brush right up to the torch, it's completely stopped me wrecking retaining caps, seems to waterproof the area that was breaking down with me on previous ones.
It really keeps the shield clean as well, brush it on cold or warm even when cutting.
One other thing I have learned (only recently even though I read about it ages ago) is not to tighten the retaining cap to tight, just light/finger tight or it seems to stop the electrode sliding in the swirl ring and causing misfire/fault.
Powermax XP45
Home built table, Candcnc DTHC 2, Dragoncut 620-4
R-Tech 210 Tig, Jasic 250 mig
Sheetcam, Scanything, Coreldraw
Table build gallery
Home built table, Candcnc DTHC 2, Dragoncut 620-4
R-Tech 210 Tig, Jasic 250 mig
Sheetcam, Scanything, Coreldraw
Table build gallery
- BTA Plasma
- 3.5 Star Elite Contributing Member
- Posts: 617
- Joined: Thu May 12, 2011 4:28 pm
Re: Those of you who regularly cut 1/2 and thicker stuff...Q.
1/2 is very easy. 1st...loop your corners if you can...where you can. 2nd bring your cut height to .090 minimum (Which is just initial height and not your running height). This will allow you to clear your slag. 3rdly run 65 amps. If you use an air cooled powermax machine cutting 1/2 at 65 amps will give you the best cut.
-
- 4 Star Elite Contributing Member
- Posts: 1184
- Joined: Tue Aug 25, 2015 12:05 pm
- Location: Central MO, USA
Re: Those of you who regularly cut 1/2 and thicker stuff...Q.
BTA Plasma wrote:2nd bring your cut height to .090 minimum (Which is just initial height and not your running height).
Matt, I'm not sure what you mean by this. How do you switch from pierce height, to "initial height" (to clear slag), and then drop to. 06 cut height? I could set. 09 as the cut height in the tool chart, and let the THC drive down to. 06, but what about layers where the THC never activates (holes)?
I will try that. I was doing the Jim Colt "lowest usable amperage will give the best angularity" thing. I'll do some practice with 65. I'd like to get away from those 9ipm holes. LolBTA Plasma wrote:3rdly run 65 amps. If you use an air cooled powermax machine cutting 1/2 at 65 amps will give you the best cut.
Bulltear 6x12 w/ Proton Z axis & watertable
CommandCNC/Linux w/ Ohmic & HyT options
Hypertherm Powermax 85 w/ machine torch
Solidworks, Coreldraw X7, Inkscape, Sheetcam
CommandCNC/Linux w/ Ohmic & HyT options
Hypertherm Powermax 85 w/ machine torch
Solidworks, Coreldraw X7, Inkscape, Sheetcam
- tnbndr
- 4.5 Star Elite Contributing Member
- Posts: 1690
- Joined: Mon Jan 09, 2012 4:30 pm
- Location: New Berlin, WI
- Contact:
Re: Those of you who regularly cut 1/2 and thicker stuff...Q.
I'm with BTA, use a higher amp 65 or 85 and I think you will find better results. I have a PM45 so I have no choice but 1/2" is at the upper limit of the 45.
Dennis
LDR 4x8, Scribe, DTHCIV
Hypertherm PM45, Macair Dryer
DeVilbiss Air America 6.5HP, 80Gal., 175psi, Two Stage
16.9scfm@100psi, 16.0scfm@175psi
Miller 215 MultiMatic
RW 390E Slip Roll (Powered)
AutoCAD, SheetCAM, Mach 3
http://ikescreations.com
LDR 4x8, Scribe, DTHCIV
Hypertherm PM45, Macair Dryer
DeVilbiss Air America 6.5HP, 80Gal., 175psi, Two Stage
16.9scfm@100psi, 16.0scfm@175psi
Miller 215 MultiMatic
RW 390E Slip Roll (Powered)
AutoCAD, SheetCAM, Mach 3
http://ikescreations.com
-
- 5 Star Elite Contributing Member
- Posts: 3087
- Joined: Mon Jul 20, 2009 11:18 pm
- Location: North Carolina
Re: Those of you who regularly cut 1/2 and thicker stuff...Q.
The 45 amp pierces great on my machine. Here are my suggestions:
-Lower the water to an inch or so below the plate......water in contact with the plate affects piercing.
-Increase lead in length or location so the slag pile will not collide with torch at end of cut.
-If you can't make a longer lead in, then do a first cut file with just all the pierces, chip the top dross off all pierces, then a second cut file to edge start on the pierces. (lower pierce height, shorter pierce delay on edge start)
-Spray anti spatter on top of plate (works if no water present)
- Use about .024" pierce height and adequate pierce delay so torch remains at pierce height til pierce is complete.
-Cut at book speed for 1/2".
I can get 300 or so pierces on a 45 Amp shielded nozzle piercing 1/2" with excellent angularity.
One bad, incorrect pierce will damage a 45 amp nozzle and cause varying angularity.
If you cannot make it work....use the 65 amp process...it is more forgiving and faster. Jim Colt Hypertherm
-Lower the water to an inch or so below the plate......water in contact with the plate affects piercing.
-Increase lead in length or location so the slag pile will not collide with torch at end of cut.
-If you can't make a longer lead in, then do a first cut file with just all the pierces, chip the top dross off all pierces, then a second cut file to edge start on the pierces. (lower pierce height, shorter pierce delay on edge start)
-Spray anti spatter on top of plate (works if no water present)
- Use about .024" pierce height and adequate pierce delay so torch remains at pierce height til pierce is complete.
-Cut at book speed for 1/2".
I can get 300 or so pierces on a 45 Amp shielded nozzle piercing 1/2" with excellent angularity.
One bad, incorrect pierce will damage a 45 amp nozzle and cause varying angularity.
If you cannot make it work....use the 65 amp process...it is more forgiving and faster. Jim Colt Hypertherm
-
- 4 Star Elite Contributing Member
- Posts: 1184
- Joined: Tue Aug 25, 2015 12:05 pm
- Location: Central MO, USA
Re: Those of you who regularly cut 1/2 and thicker stuff...Q.
Water was only 1/4" or so below the plate for me. Perhaps that was part of the problem. Noted, and I'll try this suggestion.jimcolt wrote:The 45 amp pierces great on my machine. Here are my suggestions:
-Lower the water to an inch or so below the plate......water in contact with the plate affects piercing.
I did this on the profile/exterior cuts, but didn't have that option on the 1" holes. I was piercing from hole center in order to move the slag pile as far as possible from the hole perimeter.jimcolt wrote:-Increase lead in length or location so the slag pile will not collide with torch at end of cut.
This is what I tried, with limited success. I didn't lower the pierce height during the 2nd run, though. I'll try that. Also the shorter pierce delay. If I fully pierced the material with the "pierce only" operation, the torch would have trouble establishing an arc during the "cut" operation. Perhaps the lower pierce height would address this issue.jimcolt wrote:-If you can't make a longer lead in, then do a first cut file with just all the pierces, chip the top dross off all pierces, then a second cut file to edge start on the pierces. (lower pierce height, shorter pierce delay on edge start)
I run a water table, but maybe this will help where the plate stays dry.jimcolt wrote:-Spray anti spatter on top of plate (works if no water present)
Ok. I was piercing at .20. I'll try the higher pierce.jimcolt wrote:- Use about .024" pierce height and adequate pierce delay so torch remains at pierce height til pierce is complete.
I was doing this. 18ipm on the non-holes for the 45A process, 50% (9ipm) for the holes.jimcolt wrote:-Cut at book speed for 1/2".
Yeah, I definitely learned that!jimcolt wrote:I can get 300 or so pierces on a 45 Amp shielded nozzle piercing 1/2" with excellent angularity.
One bad, incorrect pierce will damage a 45 amp nozzle and cause varying angularity.
I may go that route. These were dimensional cuts (wheel centers for mud/monster/whatever truck) with lug holes, etc. My goal was the least angularity possible, which is why I was using the 45A process (based on your advice of "lowest possible amperage provides best angularity"). Not to mention, 18ipm non-holes / 9ipm holes is very slow...jimcolt wrote:If you cannot make it work....use the 65 amp process...it is more forgiving and faster. Jim Colt Hypertherm
Bulltear 6x12 w/ Proton Z axis & watertable
CommandCNC/Linux w/ Ohmic & HyT options
Hypertherm Powermax 85 w/ machine torch
Solidworks, Coreldraw X7, Inkscape, Sheetcam
CommandCNC/Linux w/ Ohmic & HyT options
Hypertherm Powermax 85 w/ machine torch
Solidworks, Coreldraw X7, Inkscape, Sheetcam
- _Ogre
- 3.5 Star Member
- Posts: 529
- Joined: Sun Sep 15, 2013 4:26 pm
- Location: Motown
Re: Those of you who regularly cut 1/2 and thicker stuff...Q.
not sure if this is pertinent: we did a couple of 3 sheet runs of 1/2'' 7x7 plates with 9/16'' holes in each corner
i was concerned that the torch would crash mid program and we'd have to constantly reset the g-code start
i set the file to cut 3 rows of 6 plates, cutting 4 holes in each plate and then the perimeter of each plate, then modified the g-code to stop at the next start point
i avoid slag piles by setting start points to avoid conflicts and by cutting 3 rows the operator could check cut quality before hitting start again
390 pierces per 4x8 plate; i had the operator change nozzles every sheet. the cost of consumable was minimal for this sized job
we did not run the athc. all cuts were 65 amp
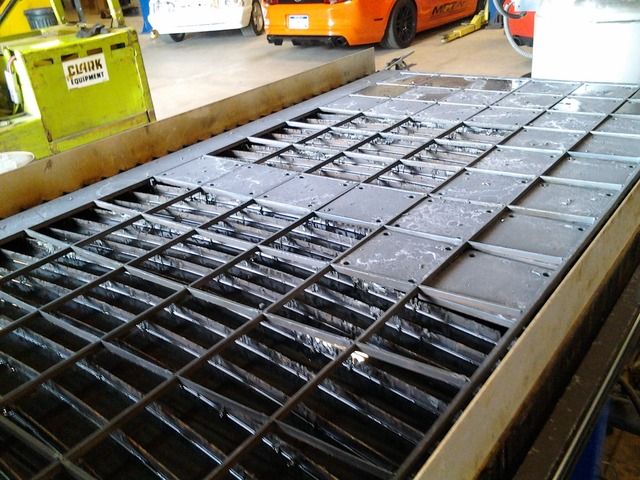
i was concerned that the torch would crash mid program and we'd have to constantly reset the g-code start
i set the file to cut 3 rows of 6 plates, cutting 4 holes in each plate and then the perimeter of each plate, then modified the g-code to stop at the next start point
i avoid slag piles by setting start points to avoid conflicts and by cutting 3 rows the operator could check cut quality before hitting start again
390 pierces per 4x8 plate; i had the operator change nozzles every sheet. the cost of consumable was minimal for this sized job
we did not run the athc. all cuts were 65 amp
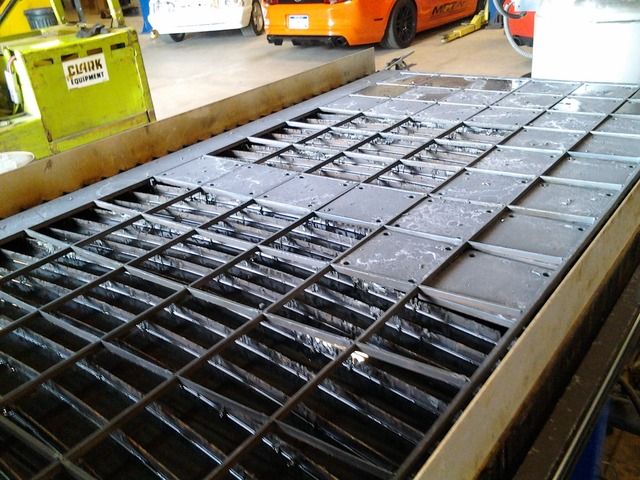
bulltear 4x8 cnc plasma table, candcnc bladerunner w/dthc, hypertherm powermax 65, sheetcam, mach3
laser cross hair for hypertherm torch http://www.plasmaspider.com/viewtopic.php?f=6&t=12508
an ogre smiley
how cool!
laser cross hair for hypertherm torch http://www.plasmaspider.com/viewtopic.php?f=6&t=12508
an ogre smiley
