Trying to cut 16ga steel with a Hypertherm Powermax 1000 with 40amp consumables and the machine set to 25 amps. Mach3 voltage for DTHC was set to 150volts (I did a few test cuts to ensure cut height was .0625" at 150V) Consumables were all new.
Seems no matter what I do the bottom side dross dues not change. It's always heavy and stuck to the metal.
Here are my test cuts where the I only change I made was feed rate. Bottom line is at F90. and each line above had 10ipm added to the speed.
top side:
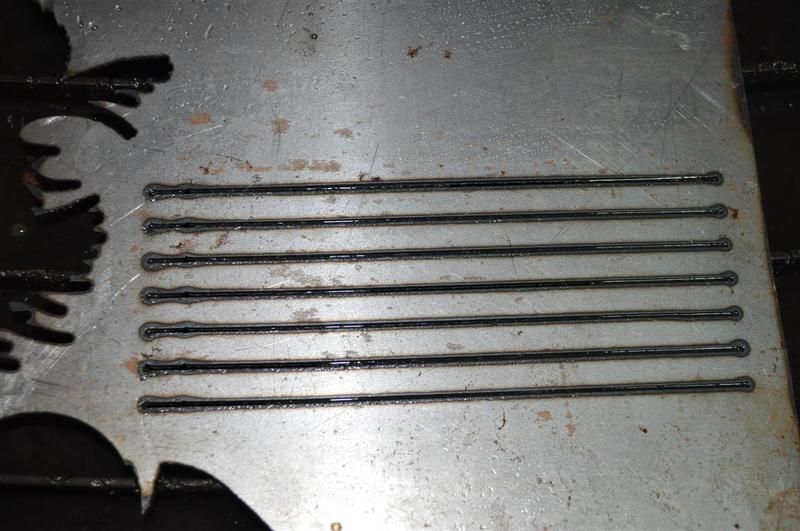
Bottom Side:
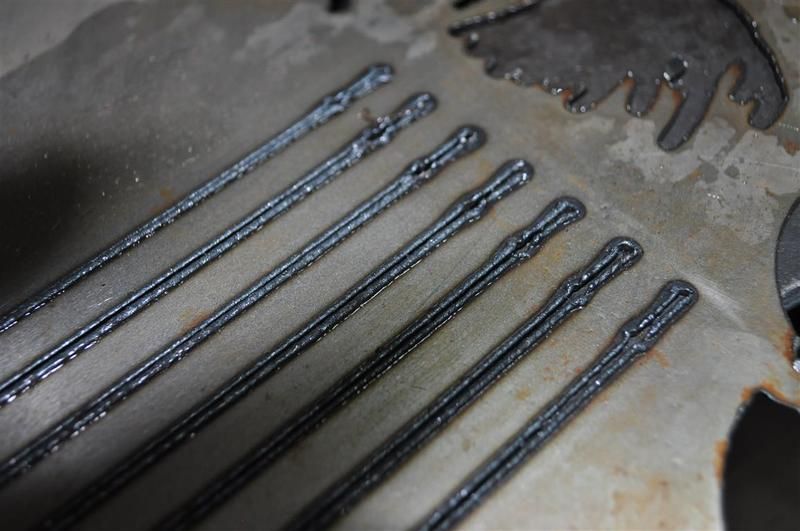
You will notice the "divot" .5" from the start. Seems anytime the program turns on the DTHC (S20) the machine pauses for .2 of a second. Haven't figured out why yet?
If I switch to fine cut consumables I can get the dross to be much more manageable. Any Ideas?