Dross on 1/4" mild steel, improvements?
-
- 3 Star Member
- Posts: 345
- Joined: Mon Feb 23, 2015 5:23 pm
- Location: Austin, TX
Dross on 1/4" mild steel, improvements?
Running Hypertherm 65, using 65 amp consumables at book settings. Using 45 amp consumables is understandably a bit cleaner, but I'm cutting thousands of these, so I'm trying to get better speed. Can I get it any cleaner than this with 65 amp consumables?
The dross removes pretty quickly with a putty knife or in my tumbler for about an hour. When using 45 amp consumables and its cleaner, I only need 30 mins in tumbler and there's less dust, so if I could improve some, that would be great.
The dross removes pretty quickly with a putty knife or in my tumbler for about an hour. When using 45 amp consumables and its cleaner, I only need 30 mins in tumbler and there's less dust, so if I could improve some, that would be great.
-
- 3 Star Member
- Posts: 445
- Joined: Sat Jul 04, 2015 10:43 pm
Re: Dross on 1/4" mild steel, improvements?
top cut was 45consumables, lower cut is 65. That is 3/8"
Steve
Platform CNC Plasma table
CandCNC Ethercut IV DTHC
Hypertherm 85/CPC/RS485
Miller 350P
Miller Dynasty 280DX
Platform CNC Plasma table
CandCNC Ethercut IV DTHC
Hypertherm 85/CPC/RS485
Miller 350P
Miller Dynasty 280DX
-
- 3 Star Member
- Posts: 345
- Joined: Mon Feb 23, 2015 5:23 pm
- Location: Austin, TX
Re: Dross on 1/4" mild steel, improvements?
Settings:
.06 cut height
.15 Pierce height
.5 pierce time
90 ipm cut speed
127 volts
CandCNC setup with DTHC IV, DTHC turned off for holes
.06 cut height
.15 Pierce height
.5 pierce time
90 ipm cut speed
127 volts
CandCNC setup with DTHC IV, DTHC turned off for holes
-
- 3.5 Star Member
- Posts: 511
- Joined: Wed Apr 23, 2014 2:48 pm
Re: Dross on 1/4" mild steel, improvements?
Water too high? Looks like it to me..
-
- 3.5 Star Elite Contributing Member
- Posts: 623
- Joined: Sat Aug 25, 2012 8:08 pm
- Location: Edmonton, Alberta Canada
- Contact:
Re: Dross on 1/4" mild steel, improvements?
My water table runs from 1/2" below( I forgot to fill up) to touching the bottom of plate. My 1/4" comes out almost no dross either way. I usually drop on floor and it is gone. 65 amp book settings .
HTH
Gary
HTH
Gary
4x8 Home made with Precision Plasma LLC. Gantry
4x8 Home Router made with Precision Plasma LLC. Gantry
Candcnc DHCTII Electronics
Hypertherm Powermax 105 machine torch
Sheetcam, Mach 3
Corel Draw 8, V Carve Pro
Miller CTS 280 Miller Mig
4x8 Home Router made with Precision Plasma LLC. Gantry
Candcnc DHCTII Electronics
Hypertherm Powermax 105 machine torch
Sheetcam, Mach 3
Corel Draw 8, V Carve Pro
Miller CTS 280 Miller Mig
-
- 3 Star Member
- Posts: 345
- Joined: Mon Feb 23, 2015 5:23 pm
- Location: Austin, TX
Re: Dross on 1/4" mild steel, improvements?
The water is at least 3/4 of an inch below, but because these pieces are tightly nested and fall through, the blow through splashes up a lot. If I lower the water, I get a lot of smoke.
I'm working on an air filter and exhaust, so maybe that won't matter soon.
I'm working on an air filter and exhaust, so maybe that won't matter soon.
-
- 5 Star Elite Contributing Member
- Posts: 3087
- Joined: Mon Jul 20, 2009 11:18 pm
- Location: North Carolina
Re: Dross on 1/4" mild steel, improvements?
Looks like the torch is too high. Shut off height control and set .06" height with feeler gauges....cut at book speed. Should be no dross, assuming the consumables are in good shape. Monitor the arc voltage readout when at a fixed height/book speed......then that is what your voltage should be under those conditions. Just looking at the bottom of the cut does not give the whole story....pics of edge striations and angularity are important for us to help. Jim Colt Hypertherm
-
- 3.5 Star Member
- Posts: 511
- Joined: Wed Apr 23, 2014 2:48 pm
Re: Dross on 1/4" mild steel, improvements?
I just cut some .250 last night with 45 amp shielded consumables.. I double checked my Torch height before I started cutting. 10ga fine cuts were having all sorts of problems.. Sure enough .020 too low on my offset.. I made a few changes, and never got back to checking that again. The Torch height voltage on the standard consumables was reading low, so I should of known something was up.. Now I am back to 137 volts, but my speed is up to 60 ipm instead on the best quality 48 the book says.. Everything else is book specs.. It's turns out good quality cuts now.. Very little dross,(little bit)but then the steel has a bit of rust on the underside too.Just what you are cutting can throw you through a loop too.
-
- 3 Star Member
- Posts: 345
- Joined: Mon Feb 23, 2015 5:23 pm
- Location: Austin, TX
Re: Dross on 1/4" mild steel, improvements?
jimcolt wrote:Looks like the torch is too high. Shut off height control and set .06" height with feeler gauges....cut at book speed. Should be no dross, assuming the consumables are in good shape. Monitor the arc voltage readout when at a fixed height/book speed......then that is what your voltage should be under those conditions. Just looking at the bottom of the cut does not give the whole story....pics of edge striations and angularity are important for us to help. Jim Colt Hypertherm
I checked it and when it starts, it seems to be right on at .06. Oddly enough, when it gets to the longer sides, the dthc lowers it to .04xx and fluctuates from .03x to .06x on the DRO. Now that I look at the picture, the two narrow ends, they are much cleaner than the longer sides.
-
- 5 Star Elite Contributing Member
- Posts: 3087
- Joined: Mon Jul 20, 2009 11:18 pm
- Location: North Carolina
Re: Dross on 1/4" mild steel, improvements?
Increase your arc voltage until the height during steady state cutting is correct. The voltage specs are correct in the Hypertherm manual with new consumables in laboratory conditions. Results in the field based on height control calibration and other factors will vary....so start with the book voltage setting then adjust so the steady state cut height is correct.Then if dross is still present increase the speed 3 to 5 ipm per test cut until the dross is gone. Jim Colt Hypertherm
-
- 3.5 Star Member
- Posts: 511
- Joined: Wed Apr 23, 2014 2:48 pm
Re: Dross on 1/4" mild steel, improvements?
If you get zero free dross, Pretty sure Bevel will increase.. I don't think best quality bevel, and no dross lands at the same IPM with .250/45 amps. Not on the pieces I cut.. The 48 ipm is too slow on my machine,for either to be in the exact right parameters.. Locked solid readings from my THC, at .060/pretty much 137 volts. You can tell the arc is hunting on the face of the cut, plus the arc is pushing way too much at 48 ipm.. I need to cut a bunch more steel, but the 60 ipm is pretty good compromise for me..
-
- 5 Star Elite Contributing Member
- Posts: 3087
- Joined: Mon Jul 20, 2009 11:18 pm
- Location: North Carolina
Re: Dross on 1/4" mild steel, improvements?
Brandx......in the original post he mentioned the dross and how he would like to get it "cleaner"....that is why I suggest 65 amps. At 45 amps the bevel will be slightly less, however there is a higher chance of dross.....depends on the steel (as I'm sure you know). One day 45 amp will cut with no dross....next day you could have a little.....though is scrapes off....I rarely need to use a grinder.
Once you get the height right....I look under the plate at the arc. Best cut edge angularity and minimal dross is when the sparks blow out slightly ahead of the cut (exothermic reaction working!). If you see the arc tailing behind the travel of the torch then you should slow down for best cut. This is true with air and oxygen plasma on steel only. Jim Colt
Once you get the height right....I look under the plate at the arc. Best cut edge angularity and minimal dross is when the sparks blow out slightly ahead of the cut (exothermic reaction working!). If you see the arc tailing behind the travel of the torch then you should slow down for best cut. This is true with air and oxygen plasma on steel only. Jim Colt
-
- 3.5 Star Member
- Posts: 511
- Joined: Wed Apr 23, 2014 2:48 pm
Re: Dross on 1/4" mild steel, improvements?
I am not complaining about having to speed up on the cuts..Just that there seems to be more bevel , and quite a bit more edge roughness when using the book's best setting settings. I think top edge rounding is coming into play with me.. So far the best is right between the best quality,and production speeds.. I can live with that.. Little bit of dross, but comes right off no problem.. I have a lot more to learn, to get where I want to be.. Some bevel, but well within acceptable standards. I know as thickness goes up it all gets better..I've seen .500 at 65 amps, and it was right at factory best settings.. I am just moving up the scale to get close on the sizes I might be cutting soon.. Once I got my Z axis right, things are coming along nicely.. My THC is very stable, and don't use any rules in Sheetcam.. There still is a learning curve on any new setup.. It was the right machine for my needs..(I like it)It's funny how a little setting makes all the difference in the world..True of most plasma's too..
-
- 3 Star Member
- Posts: 345
- Joined: Mon Feb 23, 2015 5:23 pm
- Location: Austin, TX
Re: Dross on 1/4" mild steel, improvements?
Thanks, I'll give it a shot and report back.
-
- 5 Star Elite Contributing Member
- Posts: 3087
- Joined: Mon Jul 20, 2009 11:18 pm
- Location: North Carolina
Re: Dross on 1/4" mild steel, improvements?
well...the "best quality" settings in the Hypertherm manuals are developed to be right at the edge of low speed dross.....which normally provides the best cut edge angularity. You say you get worse angularity at that speed? Then something else is wrong...slower is always squarer! Oh well....I hear something new every day!
1/4" at book speeds / height on my Powermax85 running with 45 amps shielded process.
1/4" at book speeds / height on my Powermax85 running with 45 amps shielded process.
Brand X wrote:I am not complaining about having to speed up on the cuts..Just that there seems to be more bevel , and quite a bit more edge roughness when using the book's best setting settings. I think top edge rounding is coming into play with me.. So far the best is right between the best quality,and production speeds.. I can live with that.. Little bit of dross, but comes right off no problem.. I have a lot more to learn, to get where I want to be.. Some bevel, but well within acceptable standards. I know as thickness goes up it all gets better..I've seen .500 at 65 amps, and it was right at factory best settings.. I am just moving up the scale to get close on the sizes I might be cutting soon.. Once I got my Z axis right, things are coming along nicely.. My THC is very stable, and don't use any rules in Sheetcam.. There still is a learning curve on any new setup.. It was the right machine for my needs..(I like it)It's funny how a little setting makes all the difference in the world..True of most plasma's too..
-
- 3.5 Star Member
- Posts: 511
- Joined: Wed Apr 23, 2014 2:48 pm
Re: Dross on 1/4" mild steel, improvements?
It's not always as sq. if the arc is hunting for material to cut. The cut face shows it too.. (IMO) The .500 /65 amps 30 ipm are right on the mark.. I guess I was expecting less bevel then I am seeing with .250 /45 amps , Probably in the range of yours, at least by checking with my cheap angle finder.. If you put the piece on edge, it would give a better view of how much you have. I have done better with other machines, but this is only a few cuts so far. I expect to improve on them one way or another. .190 is pretty much the same as far a the amount of bevel. I am use to having the 30 amp nozzles available, and those have way less bevel..More dross, but excellent cut face, and super low bevel. I perfected the other machine to do exactly that.. Maybe it will take some lower amp nozzles ,get that kind of performance 0n 3/16-.250 (I guess fine cuts would handle the 3/16 just fine) Like I said before, I fought bevel in those ranges forever with my one torch machine. Finally got it where it was outstanding.. I am not giving up yet,because I don't give up that easy. My thc, and motor movements are very smooth with excellent accel...also.. It's acceptable for most things as it is, but like seeing just how bevel free things can get.. For my own interest mostly..
I meant 10 ga on the fine cuts. they won't work well on .190..
Here is what I would get with 30 amp nozzles on .190. (victor 120) I can pretty much can figure out, there is no set up on the Powermax 65 that can be used and have it come out like this. .190 Not until they come out with low amp nozzles that is.. Post them up if you have a idea.. Like I said, the Powermax is a fine machine and cuts thicker material very nice, just wish it would do all materiel as well.. I understand thinner metal is harder to get very low bevel over some thicker metal, but it still kind of boils down to having the right options to get there with.. 10 ga. looks even better on the cut face, but both are excellent
I meant 10 ga on the fine cuts. they won't work well on .190..
Here is what I would get with 30 amp nozzles on .190. (victor 120) I can pretty much can figure out, there is no set up on the Powermax 65 that can be used and have it come out like this. .190 Not until they come out with low amp nozzles that is.. Post them up if you have a idea.. Like I said, the Powermax is a fine machine and cuts thicker material very nice, just wish it would do all materiel as well.. I understand thinner metal is harder to get very low bevel over some thicker metal, but it still kind of boils down to having the right options to get there with.. 10 ga. looks even better on the cut face, but both are excellent
- Attachments
-
- .190-2.jpg (144.35 KiB) Viewed 3057 times
- .190-2.jpg (144.35 KiB) Viewed 3057 times
-
- .190.jpg (142.32 KiB) Viewed 3058 times
- .190.jpg (142.32 KiB) Viewed 3058 times
-
- 3 Star Member
- Posts: 345
- Joined: Mon Feb 23, 2015 5:23 pm
- Location: Austin, TX
Re: Dross on 1/4" mild steel, improvements?
i tried upping the voltage today and it worked. I ended up at 138 instead of the book at 127. I'm on to another problem of a rounded divot where the outside cut overlaps at the end of the cut. I forgot to take a picture. I tried a different lead in of it being straight through the bottom corner instead of perpendicular then 90 degree turn and it didn't seem to help.
I'm thinking that the original issue is maybe that it was diving in the corners, dthc was recovering, fluctuatng the height. So I added a cut rule that on arcs(rounded corners) that it turn off dthc .2 before, and on .2 after. That seemed to help some, but I seemed to get small divots where it transitioned on/off. Sometimes they appeared, other times they didn't. Not sure if I have to slow it down in the corners. I wouldn't expect so since I'm only going 90, and I run other materials at 250-300 without problem.
I'm thinking that the original issue is maybe that it was diving in the corners, dthc was recovering, fluctuatng the height. So I added a cut rule that on arcs(rounded corners) that it turn off dthc .2 before, and on .2 after. That seemed to help some, but I seemed to get small divots where it transitioned on/off. Sometimes they appeared, other times they didn't. Not sure if I have to slow it down in the corners. I wouldn't expect so since I'm only going 90, and I run other materials at 250-300 without problem.
-
- 5 Star Elite Contributing Member
- Posts: 3087
- Joined: Mon Jul 20, 2009 11:18 pm
- Location: North Carolina
Re: Dross on 1/4" mild steel, improvements?
Brand X, Here are pics of 3/16" steel (this piece measured about .186" thick, and is cold rolled). I did the first cut right at the book specs with the 45 amp shielded consumables in my Powermax85 torch. Plasmacam table with advanced height control (9 years old, plasma is almost 6). I saw no reason to cut a second piece in an attempt to improve the cut. Having well developed cut specs in the operators manual saves thousands of users a lot of time developing their own specs.
Brand X wrote:It's not always as sq. if the arc is hunting for material to cut. The cut face shows it too.. (IMO) The .500 /65 amps 30 ipm are right on the mark.. I guess I was expecting less bevel then I am seeing with .250 /45 amps , Probably in the range of yours, at least by checking with my cheap angle finder.. If you put the piece on edge, it would give a better view of how much you have. I have done better with other machines, but this is only a few cuts so far. I expect to improve on them one way or another. .190 is pretty much the same as far a the amount of bevel. I am use to having the 30 amp nozzles available, and those have way less bevel..More dross, but excellent cut face, and super low bevel. I perfected the other machine to do exactly that.. Maybe it will take some lower amp nozzles ,get that kind of performance 0n 3/16-.250 (I guess fine cuts would handle the 3/16 just fine) Like I said before, I fought bevel in those ranges forever with my one torch machine. Finally got it where it was outstanding.. I am not giving up yet,because I don't give up that easy. My thc, and motor movements are very smooth with excellent accel...also.. It's acceptable for most things as it is, but like seeing just how bevel free things can get.. For my own interest mostly..
I meant 10 ga on the fine cuts. they won't work well on .190..
Here is what I would get with 30 amp nozzles on .190. (victor 120) I can pretty much can figure out, there is no set up on the Powermax 65 that can be used and have it come out like this. .190 Not until they come out with low amp nozzles that is.. Post them up if you have a idea.. Like I said, the Powermax is a fine machine and cuts thicker material very nice, just wish it would do all materiel as well.. I understand thinner metal is harder to get very low bevel over some thicker metal, but it still kind of boils down to having the right options to get there with.. 10 ga. looks even better on the cut face, but both are excellent
-
- 1.5 Star Member
- Posts: 34
- Joined: Mon Sep 19, 2011 12:35 pm
Re: Dross on 1/4" mild steel, improvements?
Jim,
I had a run of 1/4 over the weekend. This particular job did not need much focus on edge quality so I just went straight to book specs. My cuts looked great with a small ripple of dross on the bottom that VERY easily scrapped off with a gentle swipe for my good ole paint scrapper. Squareness was great.
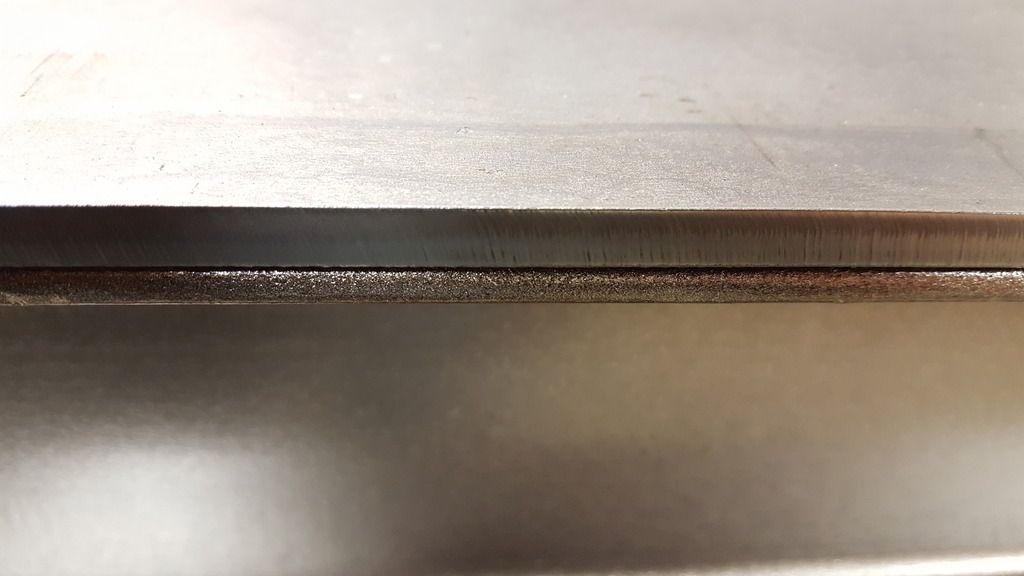
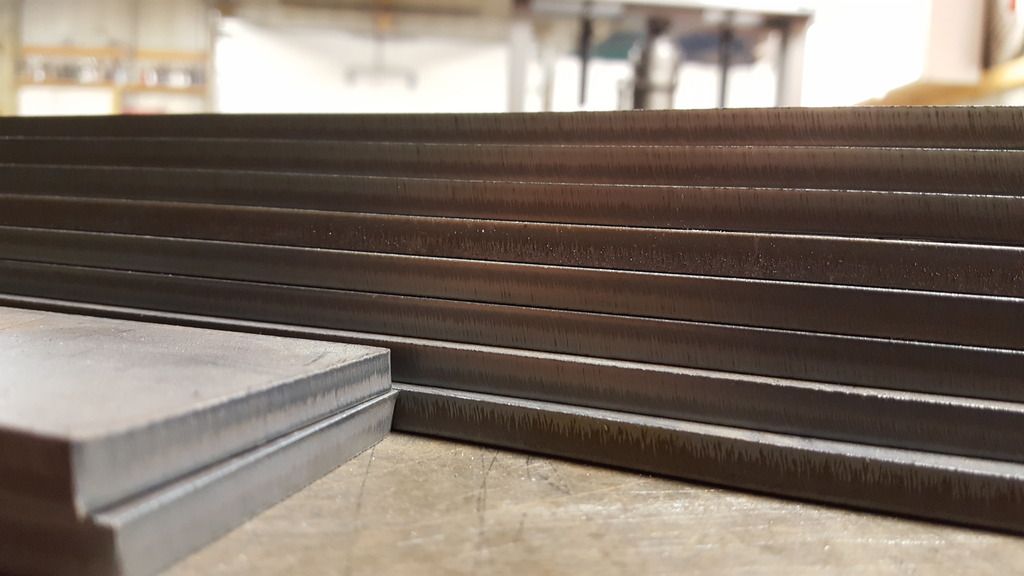
I had a run of 1/4 over the weekend. This particular job did not need much focus on edge quality so I just went straight to book specs. My cuts looked great with a small ripple of dross on the bottom that VERY easily scrapped off with a gentle swipe for my good ole paint scrapper. Squareness was great.
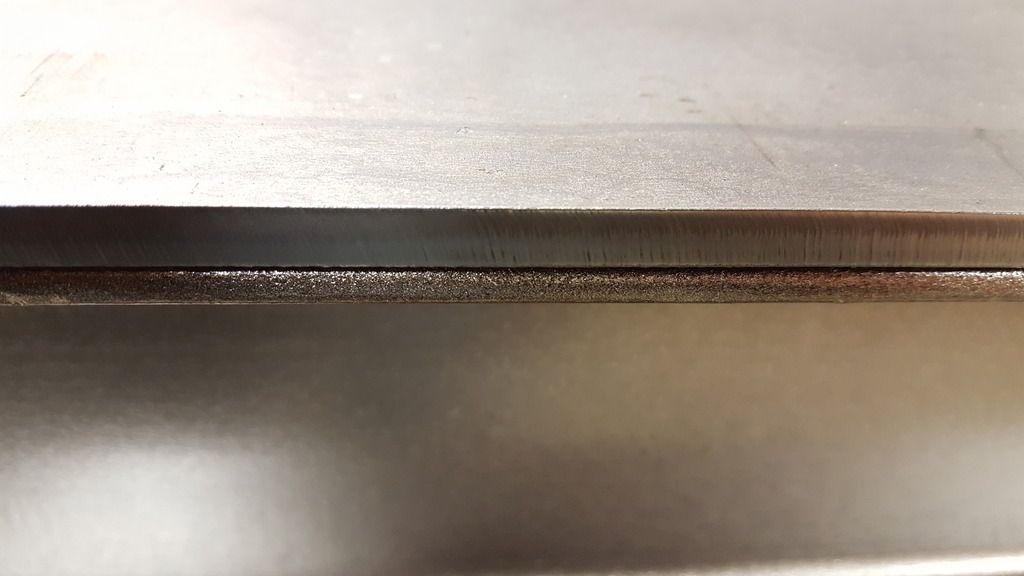
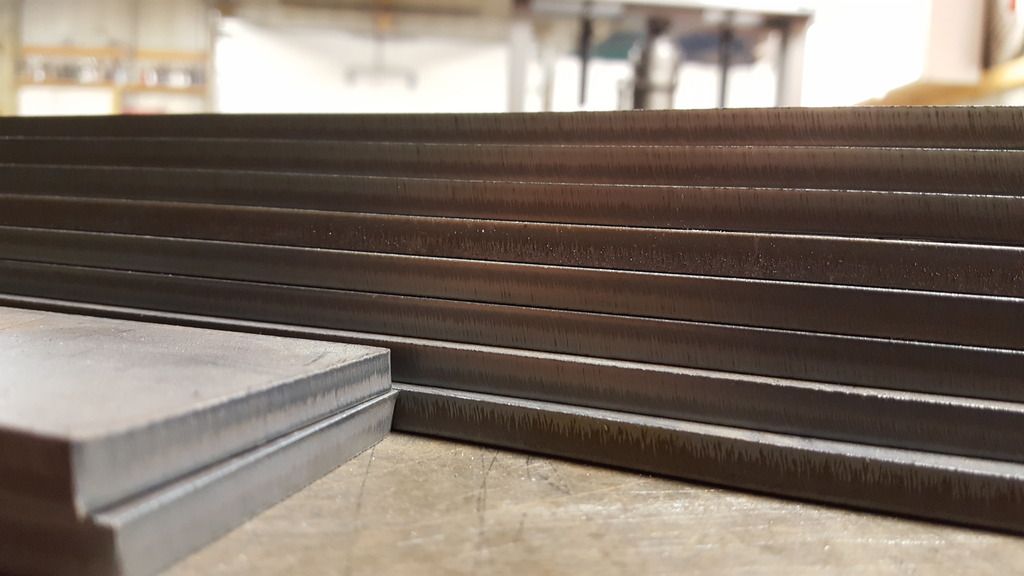
5x10 PPLLC GANTRY
PMX45
CANDCNC 620-4 OHMIC FEATHER TOUCH
VELOX Z AXIS WITH CUSTOM MOUNTS
SWAG FINGER BRAKE
ALPHATIG 200X
HOBART 210MVP
PMX45
CANDCNC 620-4 OHMIC FEATHER TOUCH
VELOX Z AXIS WITH CUSTOM MOUNTS
SWAG FINGER BRAKE
ALPHATIG 200X
HOBART 210MVP
-
- 3.5 Star Member
- Posts: 511
- Joined: Wed Apr 23, 2014 2:48 pm
Re: Dross on 1/4" mild steel, improvements?
I would still like to see a straight on view of the piece standing up.. Having it at a angle does not give me a true view on the piece.. My main issue was with 10 ga anyway. .190 is getting more on line with 45 amps (IMO)
Here is a little side note,,on other machines.. Esab's best specs for 3/16 MS at 40 amps is 64 ipm true, but did not work up low amp settings
Victor is at 50 amps is 75 ipm , very nice cuts too. Funny how the different machine are very close when it all comes out in the wash. You expect the Thermal to be slower, because of the older torch. Lot of times it's pretty dang close. when you get in the better quality range.. Each one does some thing better then the others. It's nice to have had all three current setups, just to see where the rubber meets the road. I would take the other two, and be happy also.. I certainly have way more time on the other two then the Hypertherm. I expect learn quite a bit more, with it, just like I did with the others.. The Hypertherm setting are generally very good, but not perfect for what I might want..
Here is a little side note,,on other machines.. Esab's best specs for 3/16 MS at 40 amps is 64 ipm true, but did not work up low amp settings
Victor is at 50 amps is 75 ipm , very nice cuts too. Funny how the different machine are very close when it all comes out in the wash. You expect the Thermal to be slower, because of the older torch. Lot of times it's pretty dang close. when you get in the better quality range.. Each one does some thing better then the others. It's nice to have had all three current setups, just to see where the rubber meets the road. I would take the other two, and be happy also.. I certainly have way more time on the other two then the Hypertherm. I expect learn quite a bit more, with it, just like I did with the others.. The Hypertherm setting are generally very good, but not perfect for what I might want..
-
- 5 Star Elite Contributing Member
- Posts: 3087
- Joined: Mon Jul 20, 2009 11:18 pm
- Location: North Carolina
Re: Dross on 1/4" mild steel, improvements?
Brand X OK...I just trudged out to my shop (through the snow) to get the cut sample......took a couple more pics for you to show a straight on shot of it standing. I guess the point I would make:
I agree that I could probably get a cut like this at lower power (using the Finecut consumables....or simply turning down the power with the 45 amp shielded....or unshielded consumables)......to get it as good as this one I would have to do a few experiments changing one parameter at a time (I have done this thousands of times over the last 38 years, I am very familiar) until I got the edge squareness, edge smoothness, corner quality and dross levels where I would like them. If I was lucky....I would hit perfection in 10 minutes....or it might take me an hour and a pile of coupons with sharpie notes on them.
When you can open the manual, set the numbers for height control and machine control just as the manual suggests...and get a part like this, why go through the same steps that Hypertherm already did...and did well?
I see the need for a lower power (maybe 25 amp) set of consumables for materials in the 26 gauge to maybe 10 gauge range that will allow us to slow down cut speeds and get better definition on more intricate parts. For 3/16" or .187"......we are already in pretty good shape. Jim
I agree that I could probably get a cut like this at lower power (using the Finecut consumables....or simply turning down the power with the 45 amp shielded....or unshielded consumables)......to get it as good as this one I would have to do a few experiments changing one parameter at a time (I have done this thousands of times over the last 38 years, I am very familiar) until I got the edge squareness, edge smoothness, corner quality and dross levels where I would like them. If I was lucky....I would hit perfection in 10 minutes....or it might take me an hour and a pile of coupons with sharpie notes on them.
When you can open the manual, set the numbers for height control and machine control just as the manual suggests...and get a part like this, why go through the same steps that Hypertherm already did...and did well?
I see the need for a lower power (maybe 25 amp) set of consumables for materials in the 26 gauge to maybe 10 gauge range that will allow us to slow down cut speeds and get better definition on more intricate parts. For 3/16" or .187"......we are already in pretty good shape. Jim
-
- 5 Star Elite Contributing Member
- Posts: 3087
- Joined: Mon Jul 20, 2009 11:18 pm
- Location: North Carolina
Re: Dross on 1/4" mild steel, improvements?
Here is what was written a last week (Brand X)..."Here is what I would get with 30 amp nozzles on .190. (victor 120) I can pretty much can figure out, there is no set up on the Powermax 65 that can be used and have it come out like this. .190 Not until they come out with low amp nozzles that is.. Post them up if you have a idea."
...... so I went out in my shop and cut a sample with the 45 amp shielded process from Hypertherm...it was every bit as nice as the ones Brand X posted (I think nicer...because I did not have to develop the specs....they were from the cut chart in the operators manual) .
Today Brand X says " My main issue was with 10 ga anyway. .190 is getting more on line with 45 amps (IMO ". So...I guess I'll head back out in the shop, fire up the Powermax85 and cut a piece of 10 gauge...trying book specs first!
Brand X....you are working me too hard....though I do enjoy cutting steel! Jim Colt Hypertherm
...... so I went out in my shop and cut a sample with the 45 amp shielded process from Hypertherm...it was every bit as nice as the ones Brand X posted (I think nicer...because I did not have to develop the specs....they were from the cut chart in the operators manual) .
Today Brand X says " My main issue was with 10 ga anyway. .190 is getting more on line with 45 amps (IMO ". So...I guess I'll head back out in the shop, fire up the Powermax85 and cut a piece of 10 gauge...trying book specs first!
Brand X....you are working me too hard....though I do enjoy cutting steel! Jim Colt Hypertherm
Brand X wrote:I would still like to see a straight on view of the piece standing up.. Having it at a angle does not give me a true view on the piece.. My main issue was with 10 ga anyway. .190 is getting more on line with 45 amps (IMO)
Here is a little side note,,on other machines.. Esab's best specs for 3/16 MS at 40 amps is 64 ipm true, but did not work up low amp settings
Victor is at 50 amps is 75 ipm , very nice cuts too. Funny how the different machine are very close when it all comes out in the wash. You expect the Thermal to be slower, because of the older torch. Lot of times it's pretty dang close. when you get in the better quality range.. Each one does some thing better then the others. It's nice to have had all three current setups, just to see where the rubber meets the road. I would take the other two, and be happy also.. I certainly have way more time on the other two then the Hypertherm. I expect learn quite a bit more, with it, just like I did with the others.. The Hypertherm setting are generally very good, but not perfect for what I might want..
-
- 2.5 Star Member
- Posts: 169
- Joined: Wed Jun 17, 2015 6:57 pm
Re: Dross on 1/4" mild steel, improvements?
Will 45 amp finecut work good on 1/4" steel or is the regular shielded 45 amp better? I've been cutting with 65 amp at 82 ipm with no dross, but a bit too much edge taper for my liking.
-
- 5 Star Elite Contributing Member
- Posts: 3087
- Joined: Mon Jul 20, 2009 11:18 pm
- Location: North Carolina
Re: Dross on 1/4" mild steel, improvements?
If you read my previous posts on this thread and look at the picture of the 45 amp shielded cut on 3/16"....expect very similar cut quality on 1/4". The Finecut consumables were designed to cut between 26 gauge and 10 gauge (close to 1/8" max). You could make them cut 1/4"......but I am not sure why anyone would want to. You will not beat the 45 amp shielded consumable cut quality......and the consumable life with the shielded, conical flow consumables is better than with the Finecut consumables.
The 45 amp shielded consumables using book specs on 1/4" will cut your 1/4" with far less taper than the 65 amp process.
Jim Colt Hypertherm
The 45 amp shielded consumables using book specs on 1/4" will cut your 1/4" with far less taper than the 65 amp process.
Jim Colt Hypertherm
-
- 3.5 Star Member
- Posts: 511
- Joined: Wed Apr 23, 2014 2:48 pm
Re: Dross on 1/4" mild steel, improvements?
I did try fine cuts on .190 just to see. The standard shielded 45 amp consumables are way better on every level.. I think I agree with just using standard consumables on everything except very thin metal. Where I have am heading anyway. I don't like finicky stuff, and fine cuts seem to be on 10 ga. for me..I will just turn down the amps, and deal with it that way.. I really need to get more .250 to get things sorted.. Should be real good with 45 amp stuff. Decent speed, and nice cuts. Had some .310 to try but no .250..
Jim,
thanks for putting up those pics. I will work on it a bit, and see if I can get my stuff up to snuff. Don't really care as long as I can get good results at whatever amps work for me.. I personally like 65 amps on .500 over the 45 amp. Maybe not quite as smooth cut face, but makes good parts for me.. (less dross overall, but that is never that big a deal when it comes off easy enough..
Jim,
thanks for putting up those pics. I will work on it a bit, and see if I can get my stuff up to snuff. Don't really care as long as I can get good results at whatever amps work for me.. I personally like 65 amps on .500 over the 45 amp. Maybe not quite as smooth cut face, but makes good parts for me.. (less dross overall, but that is never that big a deal when it comes off easy enough..